Предлагает услуги по пошиву одежды оптом, а именно:
пошив униформы
пошив корпоративной одежды
пошив промо формы (промо одежды)
пошив рубашек
пошив брюк
пошив юбок
пошив форменной и фирменной одежды
пошив комбинезонов и полукомбинезонов
пошив футболок и толстовок
пошив платьев и блузок
пошив жакетов и пиджаков
пошив медицинской одежды и рабочей одежды
пошив ветровок и курток
пошив пиджаков и костюмов
пошив пальто и плащей
Сбавить смесь: зачем нужна синтетика в составе. Нить синтетика
Синтетические волокна
Возможность заранее задать необходимые свойства ткани имеет очень большое значение для современной текстильной промышленности. Изделия нового поколения более адаптированы к потребностям человеческого организма, обладают многофункциональными и комфортными свойствами.
Синтетические волокна активно используются для производства спецодежды, одежды для экстремальных условий и спорта.
В настоящее время существует несколько тысяч видов синтетических волокон, и их число растет с каждым годом. Самые распространенные будут рассмотрены ниже.
Полиуретановые волокна
По механическим показателям полиуретановые волокна во многом сходны с резиновыми нитями, т.к. способны к высокоэластичным обратимым деформациям. Такие волокна придают текстильным материалам высокую эластичность, устойчивость к истиранию, упругость, формоустойчивость, несминаемость. Они редко применяются в чистом виде. Наиболее распространено их участие в ткани в качестве каркасных нитей, вокруг которых навеваются другие нити. Недостатком таких волокон является низкая термоустойчивость. Уже при 120 С полиуретановые волокна в растянутом состоянии значительно теряют прочность.
Основными представителями полиуретановых волокон являются такие торговые названия, как эластан, лайкра, спандекс, неолан и др.
Полиамидные волокна
Отличительное свойство полиамидных волокон – повышенная устойчивость к истиранию, превосходящая хлопок в 10 раз, шерсть в 20 раз, а вискозу в 50. Также отличаются высокой формоустойчивостью. Из недостатков необходимо отметить низкую устойчивость к свету и действию пота. На свету они желтеют и становятся ломкими. Кроме того, такие волокна обладают невысокой гигроскопичностью и подвержены сильному пиллингу. Однако многие их недостатки могут быть устранены путем введения различных стабилизаторов. Часто полиамидные волокна добавляются в смесовые ткани (с хлопком, шерстью, вискозой) в части, не превышающей 10-15 %, что практически не ухудшает гигиенических свойств изделий, но зато значительно улучшает механические. Волокна широко применяются в производстве чулочно-носочных и трикотажных изделий, для производства швейных ниток и галантереи.
Основные торговые названия: капрон, анид, нейлон, tactel, meryl и др.
Полиэфирные волокна
Основным свойством полиэфирных волокон является повышенная термостойкость, превосходящая показатели всех природных и большинства химических волокон. Выпуск таких волокон в настоящее время занимает лидирующее положение среди химических волокон благодаря их высоким физико-механическим показателям. Они обладают большой упругостью и высокой устойчивостью к истиранию. Ткани из таких волокон хорошо держат форму, не мнутся, имеют малую степень усадки. Недостатками являются повышенная жесткость, склонность к пилингу, сильная электризуемость и низкая гигроскопичность. Недостатки устраняются путем модификации исходного сырья. Из полиэфирных волокон в смеси с натуральными материалами (хлопок, шерсть, лен), а также вискозой успешно производятся сорочечные, плательные, костюмные и пальтовые ткани, а также искусственный мех. При этом устраняется такой недостаток как сминаемость, увеличивается прочность к истиранию при сохранении гигиенических свойств.
Торговые названия: лавсан, полиэстр, терилен и др.
Полиакрилонитрильные волокна
Такие волокна называют «искусственной шерстью» в силу близости их механических свойств. Обладают высокой светостойкостью и термостойкостью, достаточной прочностью, хорошо держат форму. Из недостатков стоит отметить низкую гигроскопичность, склонность к образованию пиллей, жесткость и электризуемость. Однако все недостатки устраняются путем модификации. В швейном деле применяются в основном при пошиве верхней одежды в смеси с шерстью, искусственного меха.
Торговые названия: нитрон, акрил, акрилан, кашмилон и др.
Полиолефиновые волокна
К этой категории относятся полиэтиленовые и полипропиленовые волокна.
Отличительной особенностью полипропиленовых волокон является их низкая плотность. Это самые легкие из всех видов волокон. Кроме того, гигроскопичность их почти равна нулю, поэтому они не тонут в воде. Такие волокна обладают хорошими теплоизоляционными свойствами. Недостатком является низкая термостойкость (115 С), который может быть нивелирован модификацией. Оптимальным является создание двухслойных материалов, в которых нижний слой выполняется из полиолефиновых волокон, а верхний – из гигроскопичных целлюлозных волокон. Такая технология позволяет нижнему слою оставаться сухим, но отводить влагу в гигроскопичный верхний слой. Часто применяется при пошиве нижнего белья, спортивных изделий, а также чулочно-носочных изделий с повышенными гигиеническими характеристиками.
Торговые названия: геркулон, ульстрен, найден, мераклон и др.
Полиэтиленовое волокно используется в основном для технических целей. Торговые названия: спектра, дайнема, текмилон.
Поливинилхлоридные волокна
Поливинилхлоридные волокна обладают высокой химической стойкостью, низкой электропроводностью и очень низкой термостойкостью (разрушаются при 100 С). При трении волокно приобретает высокий электростатический заряд, что наделяет изготовленное из него белье лечебными свойствами при лечении таких заболеваний, как радикулит, артрит. Кроме того, для таких волокон характерна высокая степень усадки после термообработки. Это свойство используется для получения красивой рельефной поверхности ткани. Помимо этого, поливинилхлоридные волокна применяются при изготовлении ворса ковров, искусственного меха, искусственной кожи.
Торговые названия: хлорин, тевирон, виньон и др.
Поливинилспиртовые волокна
Обладают прекрасным комплексом потребительских характеристик: прочные, высокая устойчивость к истиранию, высокая теплостойкость и светоустойчивость, а также повышенная гигроскопичность (в отличие от всех других синтетических волокон). Проведение модификации таких волокон позволяет получить волокна с определенными свойствами: огнестойкие, бактерицидные, ионообменные и т.д. Винол используется в производстве тканей для белья и одежды, а в смеси с хлопком и вискозой – для выработки чулочно-носочных изделий. Мтилан обладает антимикробными свойствами, широко применяется в медицине в качестве нитей для хирургических швов.
Другие торговые названия: винилон, куралон, виналон и др.
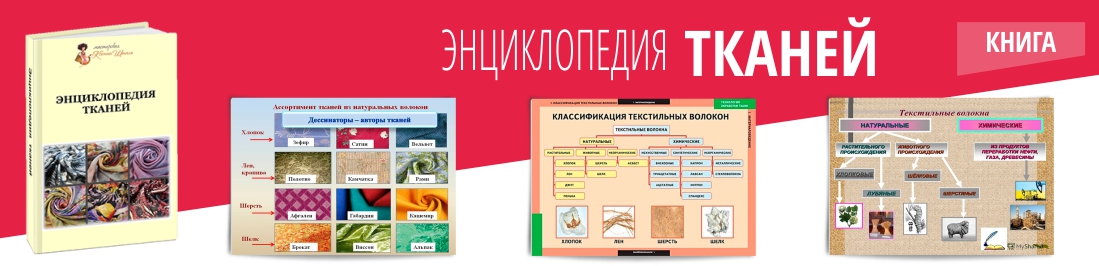
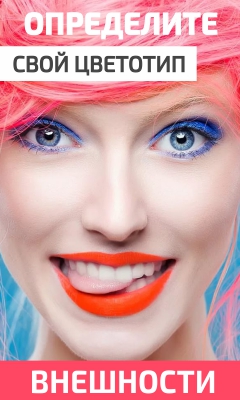
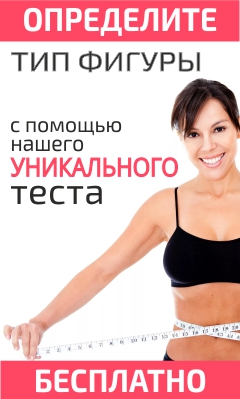
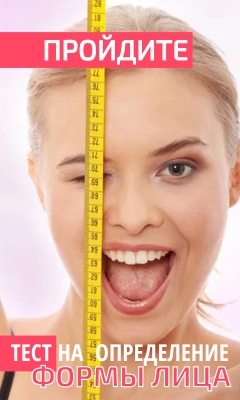
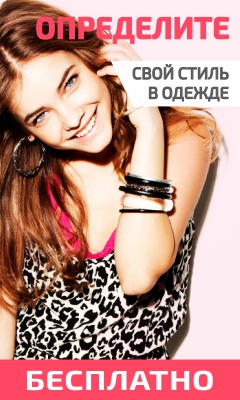
ОСТАВЬТЕ СВОЙ КОММЕНТАРИЙ И ПОЛУЧИТЕ ПОЛЕЗНЫЙ ПОДАРОК, ПОМОГАЮЩИЙ ДЕРЖАТЬ СЕБЯ ВСЕГДА В ФОРМЕ!
www.ask4style.ru
Синтетические волокна. 100 знаменитых изобретений
Синтетические волокна
На протяжении тысячелетий человечество использовало для своих нужд природные волокна растительного (лен, хлопок, пенька) и животного (шерсть, шелк) происхождения. Кроме того, применялись и минеральные материалы, например асбест.
Ткани, производимые из этих волокон, шли на изготовление одежды, технические нужды и т. п.
В связи с ростом населения Земли натуральных волокон стало не хватать. Именно поэтому возникла потребность в их заменителях.
Первую попытку получить искусственным путем шелк предпринял в 1855 г. француз Одемар на основе нитроцеллюлозы. В 1884 г. французский инженер Г. Шардоне разработал метод получения искусственного волокна – нитрошелка, и с 1890 г. было организовано широкое производство искусственного шелка нитратным способом с образованием нитей с помощью фильер. Особенно эффективным оказалось начавшееся в 90-х годах XIX в. производство шелка из вискозы. Впоследствии этот способ получил наиболее широкое распространение, и ныне вискозный шелк составляет примерно 85 % мирового производства искусственного волокна. В 1900 г. мировое производство вискозного шелка составило 985 тонн, в 1930 г. – около 200 тыс. тонн, а в 1950 г. производство вискозного шелка достигло почти 1600 тыс. тонн.
В 1920-х годах было освоено производство ацетатного шелка (из ацетилцеллюлозы). По внешнему виду ацетатный шелк почти неотличим от натурального. Он малогигроскопичен и, в отличие от вискозного шелка, не мнется. Ацетатный шелк широко применяется в электротехнике как изоляционный материал. Позже был открыт способ получения ацетатного волокна чрезвычайно большой прочности (шнур сечением в 1 см2 выдерживает нагрузку в 10 тонн).
На основе успехов химии на протяжении XX в. в СССР, Англии, Франции, Италии, США, Японии и других странах была создана мощная промышленность искусственного волокна.
Накануне Первой мировой войны во всем мире производилось всего 11 тыс. тонн искусственного волокна, а спустя 25 лет производство искусственного волокна оттеснило производство натурального шелка. Если в 1927 г. производство вискозного и ацетатного шелка составляло около 60 тыс. тонн, то в 1956 г. мировая продукция искусственных – вискозных и ацетатных – волокон превысила 2 млн тонн.
Разница между натуральным, искусственным и синтетическим волокнами состоит в следующем. Природное (натуральное) волокно полностью создано самой природой, искусственное волокно сделано руками человека, а синтетическое – создано человеком на химических заводах. При синтезе синтетических волокон из более простых веществ получают более сложные высокомолекулярные соединения, тогда как искусственные материалы образуются за счет разрушения значительно более сложных молекул (например, молекул клетчатки при получении метилового спирта путем сухой перегонки древесины).
В 1935 г. американским химиком У. Карозерсом был открыт нейлон – первое синтетическое волокно. Карозерс сначала работал бухгалтером, но позже заинтересовался химией и поступил в Иллинойский университет. Уже на третьем курсе ему поручили читать лекции по химии. В 1926 г. Гарвардский университет избирает его профессором органической химии.
В 1928 г. в судьбе Карозерса произошел резкий поворот. Крупнейший химический концерн «Дюпон де Немур» пригласил его возглавить лабораторию органической химии. Ему создали идеальные условия: большой штат сотрудников, самое современное оборудование, свободу в выборе тематики исследований.
Это было связано с тем, что за год до этого концерн принял стратегию на теоретические исследования, полагая, что они в конце концов принесут значительную практическую пользу, а следовательно, и прибыль.
Так и случилось. Лаборатория Карозерса, исследуя полимеризацию мономеров, после трех лет упорной работы добивается выдающегося успеха – получает полимер хлоропрена. На основе его в 1934 г. концерн «Дюпон» начал промышленное производство одного из первых видов синтетического каучука – полихлоропрена (неопрена), по своим качествам способного с успехом заменить дефицитный натуральный каучук.
Однако главной целью своих исследований Карозерс считал получение такого синтетического вещества, которое можно было бы превращать в волокно. Используя метод поликомпенсации, которым он занимался еще в Гарвардском университете, Карозерс в 1930 г. получил в результате взаимодействия этиленгликоля и себациновой кислоты полиэфир, который, как выяснилось позже, легко вытягивался в волокно. Это было уже большим достижением. Однако практического применения это вещество не могло иметь, так как легко размягчалось от горячей воды.
Дальнейшие многочисленные попытки получить коммерческое синтетическое волокно оказались безуспешными, и Карозерс решил прекратить работу в этом направлении. Руководство концерна согласилось закрыть программу. Однако заведующий химическим отделом воспротивился такому исходу дела. С большим трудом он убедил Карозерса продолжить исследования.
Заново обдумывая результаты своей работы в поисках новых путей ее продолжения, Карозерс обратил внимание на недавно синтезированные полимеры, содержащие в молекуле амидные группы – полиамиды. Этот выбор оказался исключительно плодотворным. Опыты показали, что некоторые полиамидные смолы, протиснутые через фильеру, сделанную из тонкого медицинского шприца, образуют нити, из которых можно изготовлять волокно. Применение новых смол казалось весьма многообещающим.
После новых экспериментов Карозерс и его помощники 28 февраля 1935 г. получили полиамид, из которого можно было вырабатывать прочное, упругое, эластичное, водоустойчивое волокно. Эта смола, выделенная в результате реакции гексаметилендиамина с адипиновой кислотой, с последующим нагреванием в вакууме полученной соли (АГ), была названа «полимер 66», так как исходные продукты содержали по 6 атомов углерода. Поскольку над созданием этого полимера трудились одновременно в Нью-Йорке и Лондоне, то волокно из него получило название «нейлон» – по начальным буквам этих городов. Специалисты-текстильщики признали его пригодным для коммерческого производства пряжи.
В течение двух следующих лет ученые и инженеры «Дюпона» разрабатывали в лабораторных условиях технологические процессы производства промежуточных продуктов полимера и нейлоновой пряжи и конструировали опытно-заводскую химическую установку.
16 февраля 1937 г. нейлон был запатентован. После многих опытных циклов в апреле 1937 г. было получено волокно для экспериментальной партии чулок. В июле 1938 г. было завершено строительство опытного предприятия.
29 апреля 1937 г., через три дня после того как Карозерсу исполнился 41 год, он ушел из жизни, приняв цианистый калий. Выдающегося исследователя преследовала навязчивая идея, что он не состоялся как ученый.
Разработка нейлона обошлась в 6 млн долларов, дороже, чем любой другой продукт общественного пользования. (Для сравнения: на разработку телевидения США потратили 2,5 млн долларов.)
Внешне нейлон напоминает натуральный шелк и приближается к нему по химическому строению. Однако по своей механической прочности нейлоновое волокно превосходит вискозный шелк примерно в три раза, а натуральный – почти в два раза.
Компания «Дюпон» длительное время строго охраняла секрет производственного процесса нейлона. И даже сама изготавливала необходимое для этого оборудование. Как сотрудники, так и оптовые продавцы товара обязательно давали подписку о неразглашении информации, касающейся «нейлоновых секретов».
Первым коммерческим изделием, поступившим на рынок, стали зубные щетки с нейлоновой щетиной. Их выпуск начался в 1938 году. Нейлоновые чулки были продемонстрированы в октябре 1939 г., а с начала 1940-го в г. Вилмингтон стало производиться нейлоновое волокно, которое трикотажные фабрики покупали для изготовления чулок. Благодаря взаимной договоренности торговых фирм чулки конкурирующих между собой производителей появились на рынке в один день: 15 мая 1940 года.
Массовое производство изделий из нейлона началось только после Второй мировой войны, в 1946 году. И хотя с тех пор появились многие другие полиамиды (капрон, перлон и др.), нейлон все еще широко применяется в текстильной промышленности.
Если в 1939 г. мировое производство нейлона составило лишь 180 тонн, то в 1953 г. оно достигло 110 тыс. тонн.
Из нейлоновой пластмассы в 50-е годы прошлого века изготавливали судовые лопастные винты для судов малого и среднего тоннажа.
В 40–50-е годы XX в. появились и другие синтетические полиамидные волокна. Так, в СССР был наиболее распространен капрон. В качестве исходного сырья для его производства используется дешевый фенол, вырабатываемый из каменноугольной смолы. Из 1 т фенола можно получить около 0,5 т смолы, а из нее изготовить капрон в количестве, достаточном для изготовления 20–25 тыс. пар чулок. Капрон получают и из продуктов переработки нефти.
В 1953 г. впервые в мире в СССР в опытно-промышленном масштабе была осуществлена реакция полимеризации между этиленом и четыреххлористым углеродом и получен исходный продукт для промышленного производства волокна энант. Схема его производства была разработана коллективом ученых под руководством А. Н. Несмеянова.
По основным физико-механическим свойствам энант не только не уступал другим известным полиамидным волокнам, но и во многом превосходил капрон и нейлон.
В 50–60-е гг. прошлого века началось производство полиэфирных, полиакрилонитрильных синтетических волокон.
Полиэфирные волокна формируются из расплава полиэтилен-терефталата. Они обладают превосходной термостойкостью, сохраняя 50 % прочности при температуре 180 °C, огнестойки и атмосферостойкие. Устойчивы к действию растворителей и вредителей: моли, плесени и т. п. Нить из полиэфирных волокон используется для изготовления транспортерных лент, приводных ремней, канатов, парусов, рыболовных сетей, шлангов, в качестве основы для шин. Моноволокно применяется для производства сетки для бумагоделательных машин, струн для ракеток. В текстильной промышленности нить из полиэфирных волокон идет на изготовление трикотажа, тканей и т. п. К полиэфирным волокнам относится лавсан.
Полиакрилонитрильные волокна по своим свойствам близки к шерсти. Они устойчивы к действию кислот, щелочей, растворителей. Их применяют для изготовления верхнего трикотажа, ковров, тканей для костюмов. В смеси с хлопком и вискозным волокном полиакрилонитрильные волокна используют для изготовления белья, гардин, брезентов. В СССР эти волокна выпускались под торговым названием нитрон.
Многие синтетические волокна получают путем продавливания расплава или раствора полимера через фильеры диаметром от 50 до 500 микрометров в камеру с холодным воздухом, где происходит отвердение и превращение струек в волокно. Непрерывно образующуюся нить наматывают на бобину.
Отвердение ацетатных волокон происходит в среде горячего воздуха для испарения растворителя, а отвердение вискозных волокон – в осадительных ваннах со специальными жидкими реагентами. Вытяжка волокон на бобинах при формировании применяется для того, чтобы цепные полимерные молекулы приняли более четкий порядок.
На свойства волокон влияют разными методами: изменением скорости выдавливания, состава и концентрации веществ в ванне, меняя температуру прядильного раствора, ванны или воздушной камеры, варьируя размеры отверстия фильер.
Важной характеристикой прочностных свойств волокна является разрывная длина, при которой волокно разрывается под действием собственной тяжести.
У природного хлопкового волокна она изменяется от 5 до 10 км, ацетатного шелка – от 12 до 14, натурального – от 30 до 35, вискозного волокна – до 50 км. Волокна из полиэфиров и полиамидов имеют большую прочность. Так у нейлона разрывная длина доходит до 80 км.
Синтетические волокна потеснили натуральные во многих областях. Общий объем их производства практически сравнялся.
Поделитесь на страничкеСледующая глава >
public.wikireading.ru
Химические нити и волокна
Искусственные нити и волокна получают из высокомолекулярных органических соединений растительного и животного происхождения, а также из неорганических соединений путем их химической переработки.
К искусственным нитям и волокнам, полученным из растительных органических соединений, относятся вискозные, полинозные, ацетатные, триацитатные и др. К нитям и волокнам из белков растительного происхождения относится зеиновое (из кукурузных семян) волокно, из белков арахиса, из белков животного происхождения казеиновое волокно. Стеклянные, металлические и другие нити и волокна относятся к неорганическим искусственным волокнам.
Синтетические волокна получают путем синтеза из природных низкомолекулярных соединений в результате реакций полимеризации или поликонденсации, в основном из продуктов переработки нефти и каменного угля.
Синтетические нити и волокна изготавливают на основе высокомолекулярных соединений (волокнообразующих полимеров) следующих видов:
Название | Химическая формула |
гетероцепные
Полиамид [ (Ch3)k CONH (Ch3)m ]n
Полиэфир
Полиуретан
карбоцепные
Полиэтилен [ Ch3 Ch3 ]n
Полипропилен [ CH Ch3 CH Ch3 ]n
Ch4 Ch4
Поливинилхлорид [ Ch3 CH ]n
Cl
Полиакрилонитрил [ Ch3 CH ]n
CN
Поливиниловый спирт [ Ch3 CH ]n
OH
Искусственные и синтетические нити получают по следующей схеме:
I. Получение и предварительная обработка сырья
На этой стадии на химических предприятиях химическими и физико-механическими методами выделяют из растений, молока, шкур животных и другого сырья волокнообразующие природные полимеры, или синтезируют полимерные вещества из низкомолекулярных органических соединений (продуктов переработки нефти: бензола, фенола, этилена, ацетилена, аммиака и др.).
II. Приготовление прядильного раствора или расплава
Полученный полимер, в зависимости от его химического состава и дальнейшей технологии переработки, переводят в раствор или расплав. Полимеры типа -целлюлозы и синтезированные гетероцепные полимеры, как правило, переводят в растворы, а синтезированные карбоцепные полимеры - в расплавы.
III. Формование волокон и нитей
Полученные прядильные растворы и расплавы продавливают через фильеры шайбы с отверстиями разной формы (круглой, треугольной, в виде звезды и др.) малого сечения (рис. 2.8). Количество отверстий фильеры определяется видом прядильного вещества (расплав или раствор) и изготавливаемой нити (элементарная нить или мононить). Количество отверстий в фильере может изменяться в пределах от 12 до 15000.
Затвердевание полимерного вещества, прошедшего через фильеру, может проходить в обдувочной шахте (рис. 2.9 а, б) или в ванне с химическим раствором (рис. 2.9 в), при взаимодействии с которым волокнообразующий полимер твердеет.
а | б | в |
Рис. 2.9. Схемы получения искусственных и синтетических волокон: а – из расплава сухим способом, б – из раствора сухим способом, в – из раствора мокрым способом |
Для придания нитям повышенной прочности после затвердевания их вытягивают в два и более раз при помощи прядильных дисков. Проведение этой операции вызывает ориентацию макромолекул полимерного вещества относительно продольной оси нити. Чем выше ориентация макромолекул, тем выше прочность и меньше деформация нитей при разрушении. После вытяжки нити сматывают на бобины.
IV. Отделка
После получения волокон и нитей проводят их отделку: с нитей и волокон после формования, особенно полученных мокрым способом, удаляют загрязнения и примеси; отбеливают для последующего окрашивания; проводят термообработку для снятия внутренних напряжений, полученных в ходе формования и вытяжки нитей; химическую обработку поверхности волокна (аппретирование, замасливание и др.), придавая свойства, необходимые для последующей текстильной переработки, и др.
Толщина и форма сечения элементарных нитей и мононитей определяется на стадии их формования в фильере и вытяжке. Длина волокон и нитей может достигать нескольких сот и тысяч метров. Для изготовления пряжи, химические нити штапелируют (нарезают), получая химические волокна длиной 50…150 мм.
Вискозное волокно получают из целлюлозы древесины ели или сосны.
Свойства: высокая прочность при растяжении (при увлажнении волокна его прочность снижается на 60%; высокая устойчивость к истиранию; высокая сминаемость; высокая гигроскопичность; сильная набухаемость и усадка; легко окрашиваются.
Модификациями вискозных волокон с улучшенными свойствами являются вискозные высокомодульные волокна (более прочные, мало теряют прочность при увлажнении), полинозные волокна (прочнее, эластичнее, мало теряют прочность при увлажнении, имеют маленькую усадку) и др.
Ацетатные и триацетатные волокна меньше сминаются, имеют низкую гигроскопичность, электризуются.
Бамбук - регенерированное целлюлозное волокно, изготовленное из мякоти бамбука. Тонкостью и белизной напоминает вискозу, обладает высокой прочностью. Бамбуковое волокно устраняет запахи, останавливает рост бактерий и убивает их. Способность бамбукового волокна останавливать рост и убивать бактерий сохраняется даже после пятидесяти стирок.Длина волокон бамбуковой пряжи составляет 15-20 см. Благодаря своей пятигранной структуре волокно отличается наличием микрополостей. Используют для наполнения подушек и одеял, для одежды.
К полиамидным волокнам (ПА) относят капрон, анид, энант. Сырьем для их получения является фенол – продукт переработки каменного угля или нефти, который после переработки превращается в капролактам (мономер полиамидной смолы). Свойства: очень высокая прочность при растяжении, стойкость к истиранию, многократному изгибу, к действию микроорганизмов, химическую стойкость, морозостойкость; низкие гигроскопичность и светостойкость (быстро желтеют на свету), высокая электризуемость и малая термостойкость. Анид и энант имеют более высокие температуры плавления, чем у капрона, большую светостойкость и превосходят его по ряду других свойств.
К полиэфирным волокнам (ПЭ) относят лавсан, получаемый на основе поликонденсации терефталевой кислоты и этиленгликоля. Свойства: достаточная упругость и эластичность, термостойкость, термопластичность; устойчивость к действию слабых кислот и щелочей; жесткость, способность к образованию пиллинга на поверхности изделия; сильная электризуемость.
Полиакрилонитрильные волокна (ПАН) называют нитроновыми. Свойства: высокая упругость, низкая теплопроводность, высокая светостойкость и термопластичность; устойчивость к действию высоких температур и гниению; мягкость, эластичность, шелковистость, пушистость практически как у шерстяных волокон.
Полиуретановые нити (ПУ) очень эластичны, упруги и несминаемы; достаточно устойчивы к светопогоде и химическим реагентам. Имеют низкую гигроскопичность. Полиуретановые нити (лайкра, спандекс и др.) придают изделиям упругость, эластичность и формоустойчивость.
Химические неорганические волокна
studfiles.net
название и виды материалов (фото)
Легкие, прочные, долговечные и красивые синтетические материалы занимают все более прочные позиции на современном текстильном рынке. За высокие эксплуатационные характеристики и низкую себестоимость синтетические ткани называют материей будущего.Синтетика – торжество химической промышленности
В сознании многих людей четко отложилась аксиома «Натуральные ткани – это хорошо, а синтетика – плохо». При этом большинство именует синтетикой все материалы, кроме хлопка, льна, шелка и шерсти.
Важно знать! Все ненатуральные ткани подразделяются на две большие группы – искусственные и синтетические. Первые производятся из природных компонентов – целлюлозы, белков, стекла. В основе синтетических материалов – только полимеры, не существующие в природе.
Синтетические волокна получают в процессе синтеза этилена, бензола или фенола, вырабатываемых из природного газа, нефти и каменного угля.
История синтетических тканей началась чуть больше полувека назад, когда незадолго до Второй мировой войны ведущим химиком американской фабрики «Дюпон» Уоллесом Карозерсом был синтезирован новый материал, получивший наименование «нейлон».
Это приятное на ощупь блестящее гладкое полотно тут же оказалось востребованным для производства дамских чулок. В годы войны нейлон шел на нужды армии, из него делали ткань для парашютов и маскировочную сетку.
Уже в конце 40-х — начале 50-х годов ХХ века началась эра синтетики – на текстильном рынке появились капрон, нитрон, анид, полиэстер и другие волокна.
Химическая промышленность не стоит на месте, и сейчас количество наименований синтетических тканей перевалило за сотню. Современные технологии позволяют получать материалы с уже заранее заданными свойствами.
Классификация синтетических волокон
Ткани из синтетических волокон различаются в зависимости от используемого при изготовлении сырья. Все современные материалы можно подразделить на несколько видов.
Полиамидные волокна
К этой группе относятся нейлон, капрон, анид и другие. Чаще всего используются для производства бытовых и технических изделий.
Отличаются высокой прочностью на растяжение и разрыв: капроновая нить в 3–4 раза прочнее, чем хлопковая. Стойки к истиранию, воздействию грибков и микробов.
Основные недостатки – низкая гигроскопичность, высокая электризуемость, устойчивость к солнечному свету. При длительном сроке службы желтеют и становятся ломкими.
Полиэфирные волокна
Самым ярким представителем этой группы синтетических материалов является лавсан, напоминающий по внешнему виду тонкую шерсть. В некоторых странах лавсан известен под названием терилен или дакрон.
Лавсановые волокна, добавленные к шерстяным, обеспечивают изделиям прочность и уменьшают их сминаемость.
Недостатком лавсана является его низкая гигроскопичность и относительная жесткость. К тому же ткань сильно электризуется.
Применяется для пошива костюмов, платьев, юбок, а также для производства искусственного меха.
Полиуретановые волокна
Главное достоинство этих волокон – эластичность и большая прочность на разрыв. Некоторые из них могут растягиваться, увеличиваясь в 5–7 раз.
Ткани, производимые из полиуретана – спандекс, лайкра, – прочные, упругие, не мнутся и прекрасно облегают тело.
Отрицательные стороны: плохо пропускают воздух, негигроскопичны, имеют низкую теплостойкость. Используются при производстве трикотажных полотен для пошива верхней одежды, спортивных костюмов, чулочно-носочных изделий.
Полиолефиновые волокна
Эти самые дешевые синтетические нити получают из полиэтилена и полипропилена. Основное использование – производство ковровых изделий, технических материалов.
Ткани, в состав которых входят полиолефиновые волокна, обладают повышенной прочностью, износостойкостью, не портятся при воздействии плесени или различных микроорганизмов.
Недостатками можно назвать значительную усадку при стирке, а также неустойчивость к высоким температурам.
Интересный факт! Не так давно было обнаружено основное достоинство полиолефиновых волокон – их способность отталкивать воду, оставаясь сухими. Благодаря этому волокна используются при производстве водоотталкивающих изделий – палаток, плащевой ткани и т. п.
Синтетический – не значит плохой
При всей своей «ненатуральности» синтетические ткани обладают рядом существенных плюсов:
- Долговечность. В отличие от «натуралов», синтетика абсолютно не подвержена гниению, воздействию плесени, грибков или различных вредителей.
- Стойкость цвета. Благодаря особой технологии, при которой ткань вначале отбеливается, а затем окрашивается, синтетика сохраняет устойчивость красок на долгие годы.
- Легкость и воздушность. Синтетические ткани весят в несколько раз меньше, чем их натуральные собратья.
- Несминаемость. Изделия из химических волокон не мнутся при носке и превосходно сохраняют форму. Синтетическую одежду можно развешивать на плечиках, не опасаясь вытягивания.
- Низкая себестоимость. Поскольку в основе производства данных тканей лежит недорогое сырье, то изделия из них доступны любым категориям покупателей.
К тому же большое многообразие синтетических тканей позволяет каждому выбрать материал исходя из своих требований и вкуса.
Без недостатков не обойтись
Хотя современная химическая промышленность и развивается семимильными шагами, пытаясь улучшать свойства синтетических материалов, все же пока от некоторых негативных сторон избавиться не удается.
Список основных недостатков синтетики:
- Пониженная гигроскопичность. Одежда из синтетики плохо впитывает влагу, нарушается теплообмен, тело человека потеет.
- Впитывание запахов. Некоторые виды тканей способны накапливать в себе неприятные запахи и распространять их вплоть до следующей стирки.
- Вероятность возникновения аллергии. У людей со склонностью к аллергическим реакциям после контакта с синтетикой может появиться раздражение на коже.
- Токсичность. К сожалению, дешевые синтетические материалы не всегда безопасны для здоровья. Не рекомендуется покупать такую одежду, в особенности для маленьких детей.
Если одежда из 100% синтетики может вызвать у покупателей вполне понятные опасения, то добавление химических волокон в натуральные ткани только улучшает их свойства, делая более безопасными и экологичными.
Важно! Материалы из смешанных волокон эластичные, не мнутся при носке, не требуют глажки, не вызывают аллергию у людей с чувствительной кожей.
Коротко о наиболее известных синтетических тканях
К самым распространенным синтетическим материям можно отнести:
- Акрил. Сырье для этой ткани получают из природного газа. По своим свойствам акрил близок к натуральной шерсти. Хорошо сохраняет тепло, поэтому из него часто шьют верхнюю одежду. Не боится моли, не выгорает на солнце и долго сохраняет яркость цвета.
Основной недостаток акрила – образование катышков при длительной носке.
- Флис. Промышленный выпуск этой ткани был налажен в 80-х годах прошлого столетия. По мягкости и удобству в носке флис сравним с натуральной шерстью или мехом.
Ткань очень легкая, эластичная, воздухопроницаемая, прекрасно сохраняет тепло. Флис неприхотлив в уходе: его можно стирать в машинке и не нужно гладить. Одежда из флиса великолепно подходит для прогулок, активного отдыха, в качестве материалов для домашних халатов и пижам.
Единственным недостатком данного материала является его способность электризоваться.
- Полиэстер. Сами по себе полиэстеровые волокна жесткие и плохо поддаются окраске. Однако в сочетании с хлопком или льном они приобретают совсем иные качества: мягкость, эластичность, устойчивость к влаге и высоким температурам.
Благодаря этим качествам полиэстеровые ткани – лучший материал для пошива штор, занавесок, домашнего текстиля – скатертей, покрывал, салфеток.
Кроме того, гладкость и шелковистость полиэстера используется при изготовлении женского нижнего белья.
- Микрофибра. Ткань была разработана в Японии и впервые увидела свет в 1975 году. Волокно настолько тонкое, что моток пряжи длиной в 100 километров весит всего пять грамм.

Микрофибра
Микрофибра хорошо стирается, быстро сохнет, долго держит форму и сохраняет цвет. Отлично впитывает влагу, поэтому чаще всего из нее делают товары для дома: салфетки, тряпочки, полотенца и т. п.
С каждым годом ассортимент синтетических тканей растет, они приобретают новые все более совершенные характеристики, стремясь удовлетворить запросы самых требовательных покупателей.
protkani.com
Синтетические волокна. Синтетическое полиамидное волокно
Синтетические волокна начали производиться промышленным способом в 1938 году. На данный момент их существует уже несколько десятков видов. Для всех них общим является то, что исходным веществом служат низкомолекулярные соединения, превращающиеся в полимеры посредством химического синтеза. Растворением или плавлением полученных полимеров осуществляется приготовление формовочного или прядильного раствора. Их формуют из раствора или расплава, а их уже потом подвергают отделке.
Разновидности
В зависимости от особенностей, которыми характеризуется строение макромолекул, синтетические волокна принято подразделять на гетероцепные и карбоцепные. К первым относят те, что получены из полимеров, в чьих макромолекулах, помимо углерода, присутствуют и иные элементы – азот, сера, кислород и другие. Сюда относят полиэфирные, полиуретановые, полиамидные и полимочевинные. Карбоцепные синтетические волокна характеризуются тем, что основная цепь у них выстроена из атомов углерода. К этой группе относят поливинилхлоридные, полиакрилнитрильные, полиолефиновые, поливинилспиртовые и фторосодержащие.
Полимеры, служащие основой для получения гетероцепных волокон, получаются посредством поликонденсации, а продукт формуется из расплавов. Карбоцепные получаются посредством цепной полимеризации, а формирование происходит обычно из растворов, в редких случаях из расплавов. Можно рассмотреть какое-то одно синтетическое полиамидное волокно, которое получило название сиблон.
Создание и применение
Такое слово, как сиблон, для многих оказывается совершенно незнакомым, однако раньше на ярлычках одежды можно было видеть аббревиатуру ВВМ, под которой скрывалось вискозное высокомодульное волокно. Тогда производителям казалось, что такое название будет выглядеть симпатичнее, чем сиблон, которое могло ассоциироваться с нейлоном и капроном. Производство синтетических волокон этого типа осуществляется из елки, как бы сказочно это не выглядело.
Особенности
Появился сиблон в начале 70-х годов прошлого века. Он представляет собой усовершенствованную вискозу. На первом этапе осуществляется получение из древесины целлюлозы, ее выделяют в чистом виде. Самое большое ее количество содержится в хлопке – около 98%, но из волокон хлопчатника и без этого получаются отличные нити. Поэтому для выработки целлюлозы чаще используется древесина, в частности хвойная, где ее содержится 40-50%, а остальное – это ненужные компоненты. От них требуется избавляться в процессе производства синтетических волокон.
Процесс создания
Синтетически волокна производятся поэтапно. На первом этапе осуществляется процесс варки, во время которой из древесной стружки все лишние вещества перемещаются в раствор, а также производится разбивка длинных полимерных цепочек на отдельные фрагменты. Естественно, тут не обходится только горячей водой, производятся добавки различных реагентов: натронов и прочих. Только варка с добавлением сульфатов позволяет получить целлюлозу, которая пригодна для производства сиблона, так как в ней остается меньше примесей.
Когда целлюлоза уже выварена, ее отправляют на отбеливание, сушку и прессовку, а потом перемещают туда, где в ней есть необходимость – это производство бумаги, целлофана, картона и волокон, то есть основное производство. Что же с ней дальше происходит?
Последующая обработка
Если требуется получить синтетические и натуральные волокна, то сначала нужно приготовить прядильный раствор. Целлюлоза представляет собой твердое вещество, которое непросто растворить. Поэтому обычно ее превращают в растворимый в воде эфир дитиоугольной кислоты. Процесс превращения в это вещество является довольно длительным. Сначала производится обработка целлюлозы горячей щелочью с последующим отжимом, в раствор при этом переходят ненужные элементы. После отжима масса измельчается, а потом помещается в специальные камеры, где начинается предсозревание – происходит укорочение молекул целлюлозы почти вдвое за счет окислительной деструкции. Далее происходит реакция щелочной целлюлозы с сероуглеродом, что позволяет получить ксантогенат. Это масса оранжевого цвета, похожая на тесто, эфир дитиоугольной кислоты и исходного вещества. Этот раствор за его вязкость получил название "вискоза".
Далее происходит фильтрование для удаления последних примесей. Выпускается растворенный воздух посредством «вскипания» эфира в вакууме. Все эти операции приводят к тому, что ксантогенат становится похож на молодой мед – желтый и тягучий. На этом прядильный раствор полностью готов.
Получение волокон
Раствор продавливается через фильеры. Искусственные синтетические волокна не просто прядутся традиционным способом. Эту операцию сложно сравнить с простой текстильной, правильнее будет сказать, что это химической процесс, позволяющий миллионам струек жидкой вискозы стать твердыми волокнами. На территории России из целлюлозы получается вискоза и сиблон. Второй тип волокна в полтора раза прочнее первого, характеризуется большей устойчивостью к щелочам, ткани из него отличаются гигроскопичностью, меньшей степенью усадки и сминания. А различия в процессах производства вискозы и сиблона появляются в тот момент, когда в осадительной ванной после фильер оказываются только что "народившиеся" синтетические волокна.
Химия в помощь
Для получения вискозы в ванну наливается серная кислота. Она предназначена для разложения эфира, благодаря чему получаются чисто целлюлозные волокна. При необходимости получения сиблона в ванну добавляют сульфат цинка, частично оказывающий препятствие гидролизу эфира, поэтому в нитях будет содержаться остаточный ксантогенат. И что же это дает? Далее волокна подвергаются растягиванию и формовке. Когда в полимерных волокнах имеются остатки ксантогената, получается вытянуть полимерные целлюлозные цепочки вдоль оси волокна, а не расположить их хаотично, что характерно для обычной вискозы. После вытяжки жгут из волокон разрезают на шпательки длиной 2-10 миллиметров. После еще нескольких процедур осуществляется прессовка волокон в кипы. Тонны древесины достаточно для получения 500 килограмм целлюлозы, из которой будет выпущено 400 килограмм волокна сиблона. Прядение целлюлозы осуществляется примерно двое суток.
Что дальше делают с сиблоном?
В восьмидесятых годах эти синтетические волокна использовались в качестве добавок к хлопку, чтобы нити прялись лучше и не рвались. Из сиблона делали подложки под искусственную кожу, а также использовали его при производстве изделий из асбеста. Тогда технологи не были заинтересованы в создании чего-то нового, требовалось как можно больше волокна для реализации задуманного.
А на Западе в те времена высокомодульные вискозные волокна использовались для производства тканей, которые отличались дешевизной и прочностью в сравнении с хлопчатобумажными, но при этом хорошо впитывали влагу и дышали. Сейчас у России не осталось собственных хлопковых регионов, поэтому на сиблон возлагаются большие надежды. Только спрос на него пока не особо велик, так как ткани и одежду отечественного производства сейчас почти никто не покупает.
Полимерные волокна
Их принято подразделять на природные, синтетические и искусственные. Природные представляют собой те волокна, образование которых осуществляется в натуральных условиях. Их принято классифицировать по происхождению, которое определяет их химический состав, на животные и растительные. Первые состоят из белка, а именно каротина. Это шелк и шерсть. Вторые состоят из целлюлозы, лигнина и гемицеллюлозы.
Искусственные синтетические волокна получаются посредством химической переработки полимеров, существующих в природе. К ним принято относить ацетатные, вискозные, альгинатные и белковые волокна. В качестве сырья для их получения служат сульфатная или сульфитная древесная целлюлоза. Выпуск искусственных волокон производится в виде текстильных и кордных нитей, а также в виде штапельного волокна, которое перерабатывается вместе с иными волокнами в процессе производства разных тканей.
Синтетическое полиамидное волокно получается из полимеров, выведенных искусственно. В качестве исходного сырья в таком процессу используются полимерные волокна, сформированные из гибких макромолекул слаборазветвленной или линейной структуры, обладающие значительной массой – более 15 000 атомных единиц массы, а также очень узким молекулярно-массовым распределением. В зависимости от типа синтетические волокна способны обладать высокой степенью прочности, значительной величиной по отношению к удлинению, эластичностью, устойчивостью к множественным нагрузкам, малыми остаточными деформации и быстрым восстановлением после снятия нагрузки. Именно поэтому помимо использования в текстиле им нашли применение в качестве армирующих элементов во время изготовления композитов, и все это позволили сделать особые свойства синтетических волокон.
Заключение
В последние несколько лет можно наблюдать очень устойчивый рост количества достижений в сфере разработки новых полимерных волокон, в частности, пара-арамидных, полиэтиленовых, термостойких, комбинированных, структура которых – ядро-оболочка, гетероциклических полимеров, в которые включены различные частицы, к примеру, серебро или иные металлы. Теперь материал нейлон – это уже не верх инженерной мысли, так как сейчас существует огромное количество новых волокон.
fb.ru
Синтетические волокна и их свойства
Синтетическими волокнами называют волокна, при получении которых происходит синтез простых молекул. К синтетическим волокнам относятся: лавсан, нитрон, капрон, хлорин, винол, полиэтиленовые, полипропиленовые и другие волокна. В зависимости от сырья получаются такие полимеры: полиамидные, полиэфирные, полиакрилонитрильные, поливинилхлоридные, поливинилспиртовые, полиуретановые. Особенностью создания химического волокна является то, что процесс формирования одновременно является и его прядением.
Полиамидные волокна. Наиболее широко распространяемые полиамидные капроновые волокна. Исходным сырьём для получения капронового волокна является бензол и фенол (продукты переработки каменного угля). На химических заводах перерабатываются в капролактан. Из капронолактана перерабатывается капроновая смола. Это расплав, который продавливается щель из фильеры выходит в виде тонких струек, которые застывают при обдувании воздухом. На одной машине может находиться 60 — 100 фильер. В зависимости от вида химического волокна фильера имеет различное количество отверстий различной величины. Волокна вытягиваются, скручиваются, обрабатываются горячей водой для фиксации структуры. Также разработаны способы получения полого капронового волокна, которое профилированное и высокоусадочное. Применяется для изготовления ткани чулочно — носочных изделий, трикотажа, швейных ниток и технического назначения. Процессы изготовления анида и энанта аналогичны с изготовлением капронового волокна.
Свойства полиамидных волокон: легкость, упругость, высокая прочность при растяжении, высокая химическая стойкость, морозостойкость, стойкость к действию микроорганизмов и плесени. Волокна растворяются в концентрированных кислотах и феноле.
Горят волокна голубоватым пламенем образуя в конце оплавленный бурый шарик.
К полиамидным относится шелок — который применяется для изготовления легких платьевых и блузочных тканей и мегалоп — химически модифицированное волокно, гигроскопическое, прочное, стойкое к истиранию, придаёт ткани повышенный мерцающий блеск. Полиамидная профилированная нить — трилобал применяется для тканей шелкового типа, близких по внешнему виду к натуральному шёлку.
Полиэфирные волокна. Лавсан вырабатывается из продуктов переработки нефти. Не меняет своих свойств в мокром состоянии.
Свойства волокон лавсана: обладают легкостью, упругостью, молестойкие, стойкие к гниению, разрушается кислотами и щелочами, гигроскопичность очень низкая 0,4%. При влажной тепловой обработке выдерживают температуру 140ºС. При внесении в пламя лавсан плавится, затем медленно горит жёлтым коптящим пламенем.
Полиуретановые волокна. По своим физико-механическим свойствам относится к эланомерам, т.е. имеет высокие показатели эластического восстановления. Разрывное удлинение 600% — 800%. При снятии нагрузки сразу эластичность восстанавливается на 90%, а через минуту — 95%. Эти волокна малогигроскопичные — 1 — 1,5%, термостойкие, стойкие к истиранию, хорошо окрашиваются. Применяются для изготовления трикотажа, лент в спортивных корсетных, и лечебных эластичных изделиях.
Полиакрилонитринные волокна (ПАН). Нитрон вырабатывается из продуктов переработки каменного угля, нефти и газа. На ощупь более мягкие и шелковистые, чем лавсан и капрон. По прочности более чем в два раза меньше прочности капронового и лавсанового волокна. Удлинение при разрыве 16 — 22%, гигроскопичность 1,5%.
Нитрон имеет ряд ценных свойств: стойкий к действию минеральных кислот, щелочей, органических растворителей при химчистке, стоек к действию бактерий, плесени, моли. По теплозащитным свойствам нитрон превосходит шерсть. При температуре 200 — 250 °С, нитрон размягчается. Горит ярким, коптящим пламенем со вспышками.
Поливинилхлоридные волокна (ПВХ). Хлорин вырабатывается из этилена или ацетилена. Обладает стойкостью к действию воды, кислот, щелочей, окислителей, не гниёт, не имеет блеска.
По теплозащитным свойствам не уступает шерсти. Прочность в мокром состоянии не меняется, имеет невысокую стойкость к светопогоде. Влажно-тепловая обработка — при 70%. Недостаток — низкая теплостойкость. Хлорин не горит, не поддерживает горение, при внесении в пламя чувствуется запах дуста, спекается. Хлорин электризуется, поэтому применяется для лечебного белья, а также для получения рельефных шёлковых тканей, искусственного меха и тканей спецодежды (рыбаков, лесников, пожарных и др.).
Стойкость к агрессивным средам, высокая механическая прочность, эластичность и другте ценные качества сделали синтетическе волокна незаменимыми для современного текстильного производства.
Понравилась заметка? Поделись!www.shweinoedelo.ru
Сбавить смесь: зачем нужна синтетика в составе
От состава ткани, из которой сшита одежда, зависит не только наш комфорт, но и внешний вид изделия. Одним из самых приятных для тела материалов является хлопок, и об этом мы знаем в буквальном смысле с детства: в нашей стране в производстве ясельной одежды разрешено использовать только натуральные ткани. Однако остальным возрастным группам потребителей отказываться от химических волокон в составе полностью не стоит: они увеличивают срок службы вещей, предотвращают сминаемость и помогают сохранить форму при стирке. В разнообразии названий «полиамид», «лайкра», «спандекс» или «нейлон», довольно легко запутаться. Разбираемся, какие волокна могут быть «замешаны» в составе ткани, зачем это нужно и, главное, в каком количестве они могут присутствовать в ткани.
Зачем нужна «синтетика»?
Синтетические добавки в тканях для одежды необходимы: они увеличивают срок службы вещей, предотвращают сминаемость ткани и помогают сохранить форму при стирке. В зависимости от типа добавляемых волокон, одежда может приобретать те или иные свойства. Нужно понимать, что изделие, полностью сделанное из синтетических волокон, комфортным быть не может. Важно, чтобы производитель корректно указывал состав на этикетке, ведь в случае с синтетическими волокнами лучше добавить меньше, чем больше. Оптимальным считается добавление до 30% синтетических волокон к хлопку и до 55% к шерсти.
ВАЖНО! Многие ошибочно называют синтетикой всё, кроме хлопка, льна, шелка и шерсти. Это не совсем верно. Химические волокна делятся на искусственные и синтетические. Искусственные волокна производят из природных видов сырья растительного происхождения (например, целлюлозы) путем их искусственной переработки. Свойства искусственных волокон очень похожи на свойства натуральных. К таким волокнам, например, относят вискозу: легкие вещи из этого материала можно смело носить и летом как альтернативу натуральным тканям. Синтетические волокна получают из продуктов переработки нефти, угля и природного газа с помощью химического синтеза. Их объединяют общим понятием «химические волокна» или «синтетические волокна». Наиболее популярные названия, которые у всех на слуху, – это «полиэстер», «полиамид», «акрил», «эластан».
Справка. Необходимо помнить, что синтетические волокна производятся из продуктов переработки нефти с применением разнообразных химических компонентов. В производстве используются летучие токсичные компоненты, часть из которых потенциально может попасть и в конечное изделие. В таком случае ни стирка, ни глажка, ни сушка не очистят ткань полностью. Поэтому одежда с преобладанием синтетических волокон противопоказана аллергикам, страдающим астмой, экземой или псориазом.
Полиэфирные волокна
Полиэфирные волокна, или просто ПЭ, – одна из самых популярных синтетических добавок в одежде. Ткани с добавлением таких волокон хорошо держат форму, не мнутся, отличаются низкой степенью усадки и долго служат. Из недостатков – изделия с преобладанием синтетических волокон сильно электризуются и плохо впитывают влагу.
Торговые названия: лавсан, полиэстер, терилен и др.
Для какой одежды? Из полиэфирных волокон в смеси с натуральными материалами (хлопок, шерсть, лен) шьют рубашки, платья, костюмы и пальто. Даже небольшое добавление этих волокон значительно улучшает свойства ткани: она меньше мнется и становится прочнее.
Полиуретановые волокна
Полиуретан – название, которое наверняка знакомо автолюбителям: именно из этого материала делают покрышки на колеса. Полиуретан нашел применение и в производстве одежды. Волокна придают материалам высокую эластичность, упругость, несминаемость, а что не менее важно – прочность.
Торговые названия: эластан, лайкра, спандекс, неолан и др.
Для какой одежды? Волокна добавляют в узкие брюки и джинсы для так называемого эффекта push-up. Всего 2% лайкры достаточно для придания изделию слегка облегающей формы, при этом в спортивных костюмах и купальниках ее содержание может достигать 20-30%.
Полиакрилонитрильные волокна
За схожие свойства эти волокна часто называют искусственной шерстью. Несомненный плюс – пряжа с добавлением полиакрилонитрильных волокон значительно легче обычной шерсти, что позволяет создавать теплые и легкие вещи. Изделие не выцветает на свету, выдерживает высокие температуры и отличается сравнительно хорошей прочностью.Торговые названия: нитрон, акрил, акрилан, кашмилон и др.
Для какой одежды? Полиакрилонитрильные волокна часто смешивают с шерстью в свитерах, кардиганах и водолазках, чтобы изделие не было слишком тяжелым. Из чистого акрила вяжут варежки, носки и теплые колготки.
Полиамидные волокна
Отличительным свойством полиамидных волокон является повышенная устойчивость к истиранию, превосходящая хлопок в 10 раз, шерсть – в 20, а вискозу – в 50. Из недостатков отмечают низкую устойчивость к свету: на свету волокна желтеют и становятся ломкими. Как и большинство синтетических волокон, они обладают невысокой гигроскопичностью и могут преподнести неприятный сюрприз в виде образования катышков, или по-научному – пиллей.
Торговые названия: капрон, нейлон, tactel (тактель), meryl (мерил) и др.
Для какой одежды? Часто полиамидные волокна добавляют в смесовые ткани (с хлопком, шерстью, вискозой) в размере, не превышающем 10–15%. Это позволяет значительно повысить прочность изделия, не ухудшая комфорт. Капрон и нейлон широко применяется в производстве чулок, носков, платьев, свитеров и ветровок.
Как показали веерные исследования Роскачества мужских рубашек, фальсификация состава тканей – практика достаточно распространенная. Как правило, причина этого нарушения имеет экономические корни. Покупая продукцию из более дорогого «80-процентного хлопка», потребитель иногда получал почти 80-процентную синтетику. Результаты исследования опубликованы здесь.
roskachestvo.gov.ru