Предлагает услуги по пошиву одежды оптом, а именно:
пошив униформы
пошив корпоративной одежды
пошив промо формы (промо одежды)
пошив рубашек
пошив брюк
пошив юбок
пошив форменной и фирменной одежды
пошив комбинезонов и полукомбинезонов
пошив футболок и толстовок
пошив платьев и блузок
пошив жакетов и пиджаков
пошив медицинской одежды и рабочей одежды
пошив ветровок и курток
пошив пиджаков и костюмов
пошив пальто и плащей
Сварные швы: классификация, типы сварочных соединений. Типы швов
Разновидности и способы выполнения сварочных швов
Конечная цель любого сварщика – получение качественного сварочного шва. От этого зависит прочность и долговечность соединения деталей. Для успешной работы важно правильно выполнить подключение; выбрать силу тока, угол наклона электрода; хорошо владеть техникой выполнения шва. Результатом правильной работы будет надежное сваривание металлических деталей.
Наклон электрода
Сварочные швы классифицируют по нескольким признакам. Виды и типы сварочных соединений нужно рассматривать последовательно, вникая в тонкости процесса. НА шов влияет расположение, направление и траектория движения электрода.
После закрепления выбранного электрода в фиксаторе, установки тока, подключения полярности начинается процесс сваривания.
У каждого мастера есть свой предпочтительный угол наклона электрода. Многие считает оптимальным значение 70 ° от горизонтальной поверхности.
От вертикальной оси при этом образуется угол, равный 20 °. Некоторые работают под максимальным углом 60 °. В целом, в большинстве учебных рекомендаций присутствует диапазон значений от 30 ° до 60 ° от вертикальной оси.
В определенных ситуациях, при сварке в труднодоступных местах, нужно ориентировать электрод строго перпендикулярно относительно поверхности свариваемого материала.
Перемещать электрод можно тоже по-разному, в противоположных направлениях: от себя или к себе.
Если материал требует глубокого прогрева, то электродом ведут к себе. В след за ним в направлении сварщика тянется рабочая зона. Образующийся шлак накрывает место сплава.
Если работа не предполагает сильного прогревания, то электрод перемещают от себя. За ним «ползет» сварочная зона. Глубина разогрева при таком исполнении шва минимальна. С направлением вопрос ясен.
Траектория движения
Особое влияние на шов оказывает траекторию движения электрода. Она в любом случае имеет колебательный характер. Иначе две поверхности сшить не удастся.
Колебания могут быть похожи на зигзаги с разным шагом между острыми углами траектории. Они могут быть плавными, напоминающими движение по смещенной восьмерке. Траектория может быть подобна елочке или прописной букве Z с вензелями вверху и внизу.
Идеальный шов имеет постоянную высоту, ширину, равномерный внешний вид без дефектов в виде кратеров, подрезов, пор, непроваров. Название возможных изъянов говорит само за себя. Хорошо отработав умения, можно успешно накладывать любой шов, сваривать разнообразные металлические детали.
Нормативы и понятие катета
Сварной шов начинает формироваться в рабочей зоне при расплавленном состоянии металлов, и окончательно образуется после застывания.
Существующая классификация группирует швы по различным признакам: типу соединения деталей, образующейся форме шва, его протяженности, количеству слоев, ориентации в пространстве.
Типы возможных сварных соединений отображены в стандарте для ручной и дуговой сварки ГОСТ 5264. Соединения, выполняемые дуговой сваркой в атмосфере защитного газа нормированы документом ГОСТ 14771.
В ГОСТах имеется обозначение каждого сварного соединения, а также таблица, содержащая основные характеристики, в частности значения катета сварочного шва.
Что такое катет, понять достаточно просто, взглянув на рисунок соединяемых деталей. Это сторона умозрительного равнобедренного треугольника максимальных размеров, который поместится в поперечном сечении шва. Правильно рассчитанное значение катета гарантирует прочность соединения.
У деталей неравномерной толщины за основу берут площадь сечения детали в самой тонкой ее части. Не следует пытаться неоправданно увеличивать катет. Это может привести к деформации сваренной конструкции. К тому же увеличится расход материалов.
Проверка размеров катета проводится с помощью универсальных справочных шаблонов, представленных в специальной литературе.
Виды соединений
В зависимости от взаимного расположения деталей сварочные соединения происходят:
- встык;
- внахлест;
- угловым способом;
- тавровым способом.
При сварке встык приваривают торцы двух деталей, расположенных в одной плоскости. Стык может выполняться с отбортовкой, без скоса и со скосом. Форма скоса может напоминать буквы Х, К, V.
В некоторых случаях сварку делают внахлест, тогда одна деталь частично водружена на другую, расположенную параллельно. Совмещенная часть является нахлестом. Сваривание при этом делают без скоса с двух сторон.
Часто появляется необходимость сделать сварной угол. Такое соединение относят к угловому типу. Оно всегда выполняется с двух сторон, может не иметь скосов или иметь скос на одной кромке.
Если сварные части образовали в результате букву Т, значит было сделано тавровое соединение. Иногда детали, сваренные тавровым швом, образуют острый угол.
В любом случае одна деталь приваривается при этом к боковой части другой. Сваривание проводят с двух сторон без скоса или со скосами с каждой стороны.
Форма и протяженность
Форма шва может быть выпуклой, ровной (плоской). Иногда появляется необходимость сделать вогнутую форму. Выпуклые соединения предназначены для усиленной нагрузки.
Вогнутые места сплавов хорошо выдерживают динамические нагрузки. Универсальностью характеризуются плоские швы, которые делают чаще всего.
По протяженности швы бывают сплошными, не имеющими интервалов между сплавленными соединениями. Иногда достаточно швов прерывистого типа.
Интересной промышленной разновидностью прерывистого шва является соединение, которое образует контактная шовная сварка. Делают ее на специальном оборудовании, оснащенном дисковыми вращающимися электродами.
Часто их называют роликами, а такой вид сварки – роликовой. На таком оборудовании можно выполнять также сплошные соединения. Полученный шов очень прочен, абсолютно герметичен. Способ используют в промышленных масштабах для изготовления труб, емкостей, герметичных модулей.
Слои и расположение в пространстве
Шов металла может состоять из валика, сделанного за один проход. В этом случае он называется однослойным. При большой толщине свариваемых деталей выполняют несколько проходов, в результате которых последовательно образуются валики один на другом. Такое сварочное соединение называется многослойным.
Учитывая многообразие производственных ситуаций, при которых происходит сварка, понятно, что сориентированы швы в каждом конкретном случае по-разному. Бывают швы нижние, верхние (потолочные), вертикальные и горизонтальные.
Вертикальные швы проваривают обычно снизу верх. Применяется траектория перемещения электрода по полумесяцу, елочке или зигзагом. Начинающим сварщикам удобнее перемещать полумесяцем.
При горизонтальной сварке делают несколько проходов от нижней кромки соединяемых деталей до верхней кромки.
В нижнем положении проводят сварку встык или любым угловым способом. Хороший результат дает сварка под углом 45 °, «в лодочку», которая может быть симметричной и несимметричной. При сваривании в труднодоступных местах лучше применять несимметричную «лодочку».
Сложнее всего проводить сварку в потолочном положении. Для этого нужен опыт. Проблема заключается в том, что расплав пытается стечь из рабочей зоны. Чтобы этого не случилось, сварку проводят короткой дугой, силу тока уменьшают на 15-20 % по сравнению с обычными значениями.
Если толщина металла в месте сварки превышает 8 мм, то нужно выполнить несколько проходов. Диаметр первого прохода должен равняться 4 мм, последующих — по 5 мм.
В зависимости от ориентации шва выбирают соответствующее положение электрода. Для выполнения горизонтальных, вертикальных, потолочных соединений, сварки неповоротных стыков труб электрод направляют углом вперед.
При сварке угловых и стыковых соединений электрод направляют углом назад. Труднодоступные места проваривают электродом под прямым углом.
Обработка сварного соединения
При проведении сварки образуются шлаки. Если шлаковые включения попадают в шов, его качество ухудшается. Все шлаковые наслоения обязательно следует зачистить.
Если сварка выполняется несколькими проходками, то зачистка швов выполняется после каждого этапа сварки. При этом используют любые способы. Сначала сваренные детали оббивают молотком и чистят жесткой щеткой.
Затем проводят грубую зачистку. Мелкие детали чистят специальными ножами или шлифовальными кругами. Крупные болванки чистят на станках. На завершающей стадии место сварного соединения полируют.
Часто для этого применяют фибровый круг шлифовальной машины. Существуют другие способы полировки сварных соединений.
Сварочное дело постоянно развивается. Появляются новые материалы, совершенствуется технология. Необходимо следить за новостями в сварочном деле, чтобы узнавать много нового и интересного.
svaring.com
Типы сварных соединений и виды сварных швов по ГОСТ
Качество сварного соединения напрямую зависит от типа выбранного шва, электрода и режима работы аппарата. Для этого рекомендуется руководствоваться действующими нормативами, а в частности — ГОСТ 5264-80. В нем подробно описаны характеристики и типы сварных соединений и виды сварных швов. По ГОСТ предъявляются особые требования к выполнению работ.
Стыковые
Наиболее популярный тип соединения, так как он характеризуется минимальным напряжением металла, простотой исполнения и надежностью. В зависимости от толщины свариваемой кромки она может быть обрезана под прямым или косым углом. Также допустимо применение одностороннего скоса.
Преимущества стыковых сварочных швов:
- минимальный показатель расхода основного и сварочного металла;
- оптимальное время сварки;
- хорошее качество соединений.
Последнее достигается только при соблюдении технологии. Угол скоса может варьироваться от 45° до 60°. Это зависит от толщины металла. Подобная геометрия применяема для листов от 20 мм и более. Также учитываются характеристики материала.
Нахлесточные
Формирование соединения методом наложения листов друг на друга актуально для толщины металла в пределах от 8-12 мм. При этом в отличие от стыковой сварки нет необходимости обрабатывать поверхность — достаточно ровно обрезать заготовку. Важно правильно рассчитать величину нахлеста.
Особенности нахлесточного сварного соединения:
- увеличен расход основного и наплавленного материала;
- шов формируется между поверхностью одного листа и торцом другого;
- область применения — точечная, роликовая и контактная сварка.
Перед началом работ листы нужно выровнять, чтобы обеспечить плотный прижим.
Тавровые
Это т-образное соединение, при котором торец одного из листов приваривается к плоскости другого. Для надежности на первом можно сделать одно или двухсторонние скосы. С их помощью увеличивается объем наплавленного металла. Область применения – дуговая сварка металлоконструкций сложной формы.
Перед началом работ нужно учесть следующие факторы:
- расположение свариваемых элементов – верхнее, боковое или нижнее;
- рекомендуемый зазор между стыками 2-3 мм для лучшего соединения;
- стандартное расположение швов – двухстороннее.
- односторонние формируются только при отсутствии возможности обработки стыка с двух сторон.
Конфигурация скосов стандартная, угол зависит от толщины металла.
Угловые
Применяются для соединения двух элементов конструкции под определенным углом. В отличие от таврового соединения наличие зазора недопустимо. Надежность обеспечивается с помощью скосов и большого объема направленного металла.
Специфика угловых сварных швов:
- необходима подготовка поверхности – формирование скосов простой или сложной конфигурации;
- для тонкостенных заготовок допускается одностороннее соединение;
- учитывается геометрия сварного шва.
Подобный способ чаще всего применяется для изготовления резервуаров или аналогичных им по форме конструкции.
Вспомогательные сварные швы
Кроме вышеописанных основных способов соединения стальных элементов в ГОСТ предусмотрены вспомогательные. Они могут применяться для формирования надежного шва с учетом требуемых эксплуатационных качеств изделия.
В зависимости от специфики шва применяются следующие методики формирования сварного стыка:
- Прорезные. Необходимы для достижения максимального показателя надежности. В одном из материалов делают углубление для установки другого листа.
- Торцовые. Относятся к категории боковых. Листы накладываются друг на друга, швы делаются на торцах конструкции.
- С накладками. Рекомендуется для конструкций со сложной конфигурацией поверхности. Применяется специальная накладка, обеспечивающая соединение двух компонентов.
- С электрозаклепками. Процесс формирования соединения аналогичен традиционному заклепыванию. Разница заключается в том, что отверстие заполняется наплавленным металлом.
Выбор того или иного сварного шва зависит от конечного результата – надежности и долговечности соединения.
ismith.ru
Основная классификация сварных швов для разных видов сварки
Сварочный шов – это участок соединения двух частей в единое целое, благодаря расплавлению металла под воздействием высокой температуры и дальнейшей его кристаллизации. На сегодняшний день различают более 100 типов соединений. Они все разделяются по особым параметрам и делятся на различные группы и подгруппы, в связи с чем и существует множество классификаций сварных швов.
Содержание статьи
По виду сварного соединения
Классификация сварных швов по виду сварного соединения делится на стыковые и угловые. Какое именно произвести соединение в той или иной ситуации, решает мастер, отталкиваясь от положения деталей в пространстве.
- Швы угловые производятся тогда, когда заготовки находятся по отношению друг к другу под углом.
- Сварка стыковых соединений образуется в результате прилегания двух частей или деталей торцами друг к другу, которые располагаются на одной плоскости. Сама дорожка при этом может быть трех видов – вогнутая, выпуклая или плоская. Последняя применяется чаше всего, так как она не имеет особо выраженного перехода на стыке деталей, что выглядит более естественно, в сравнении с остальными двумя типами. Такой метод чаще всего используется при электродуговой сварке на низких токах, чтобы не пропалить заготовку. Например, тонколистовая сталь – идеальный материал для применения сварки стыковых соединений.
- Прорезной (электрозаклепочный) производится в отверстии, которое имеется на детали и выполняется в виде точечных заклепок. То есть, при этом не образуется сварная ванна и шов результате, а детали спаиваются небольшими участками через пазы в заготовке.
По месту выполнения сварки
Классификация сварных соединений и швов данной категории зависит от положения свариваемых деталей в пространстве. Например, если нужно починить деталь какой-то конструкции, которую нельзя снять и положить, но она при этом находится на некотором расстоянии от пола, то работу мастер будет производить потолочным,нижним, горизонтальным или вертикальным соединением, отталкиваясь от размещения этой детали.
- Горизонтальные – это сварные швы, которые тянутся слева направо (или наоборот) на вертикальной детали. Чтобы при этом масса металла не стекала вниз, необходимо правильно подобрать скорость движения электродом или горелкой и силу тока (это подбирается для каждого случая в индивидуальном порядке, отталкиваясь от типа сварки, характеристик деталей и мастерства специалиста).
- Вертикальный метод производства стыковых швов ведется на вертикально расположенных заготовках, при этом швы ведутся сверху вниз (или наоборот). Сложность данного процесса заключается в том, что срабатывает сила притяжения Земли и расплавленная металлическая масса все время стекает вниз, что портит и качество и внешних вид детали. Такое соединения рекомендуется проводить в крайних случаях и только тем мастерам, у которых уже есть определенный теоретический и практических багаж знаний для работы такими дорожками. Подробнее с технологией вертикального шва можно ознакомиться тут.
- Потолочным называется положение, при котором деталь находится выше головы мастера, что намного усложняет процесс. При осуществлении потолочных сварочных швов нужно строго соблюдать правила безопасности и технологию выполнения сварки, потому что в данном случае опасность заключается в стекании массы расплавленного металла.
- Нижние способы сварки выполняются тогда, когда деталь располагается внизу по отношению к мастеру. Это самый удобный метод соединения, так как металл не растекается по сторонам или вниз, а стекает в кратер. Кроме этого, свободно выходят газы и шлаки на поверхность. Стыковое сварное соединение в нижнем положении выполняется формированием валиков на протяжении всего стыка деталей. При этом технология сварки простая – достаточно вести электрод или горелку прямо или зигзагом для создания надежной и эстетически привлекательной дорожки.
По конфигурации
Данная категория стыковых швов используется при ручной дуговой сварке электродом. Сюда относятся три типа сварочных швов – прямолинейные, криволинейные и кольцевые (спиральные). Они производятся вне зависимости от положения рабочего изделия. Все типы швов данной классификации предполагают, как стыковое, так и нахлесточное сварное соединение.
По протяженности
Классификация сварных швов по протяженности бывает двух видов: сплошные или прерывистые.
- Прерывистый – это такой шов, который производится определенной длины с синхронным интервалом. Он, в свою очередь, делится на два типа – цепная дорожка и шов в шахматном порядке. Например, двусторонние прерывистые соединения на одной стороне стенки расположены против сваренных участков шва с другой ее стороны. Такие типы сцепления могут быть как односторонними, так и двусторонними. То есть, деталь спаивается с двух сторон. Расстояние между этими сварными отрезками называется «сварочный шаг».
- Сплошные способы сварки также делятся на короткие и длинные дорожки, и совершаются вдоль всей заготовки.
- Точечный способ стыковых швов значительно отличается от других, за счет того, что здесь нет сварочной ванны и дорожки. В этом случае заготовки соединяются точками, за счет нахлесточного сварного соединения. Такой способ зачастую применяется для пайки тонкого металла или аккумуляторов.
Способы протяженных швов: а) сплошной б) прерывистый, в) точечный, г) прерывистый шахматный, д) прерывистый сплошной (цепной)
По технологии выполнения
В зависимости от технологии, по которой производится скрепление, выделяют основные четыре вида:
- Подварочный, где — меньшая часть двухстороннего шва, выполняется предварительно для предотвращения прожогов при последующей сварке;
- шов-прихватка позволяет фиксировать детали, которые уже расположены для сварки;
- временный шов необходим, чтобы скрепить заготовки на некоторое время, а по окончанию работ он удаляется.
- монтажный сварной шов, используется во время монтажа различных конструкций.
По отношению к направлению действующих усилий
Сварка стыковых соединений содержит еще одну важную классификацию, в зависимости от отношения к направлению усилий:
- Продольный способ создания стыка (фланговый), при котором усилие действует параллельно оси дорожки;
- Поперечный метод (лобовой) сварного шва, при котором его ось находится перпендикулярно (90 градусов) к оси усилия;
- Комбинированное соединение сваркой включает в себя одновременно и фланговый и поперечный тип;
- Косой, при котором ось шва располагается под углом к направлению действующих усилий.
По форме наружной поверхности
По форме поверхности сцепления делятся на три основных типа:
- Выпуклые (усиленные)- это многослойные швы, применяемый в сцеплениях при статических нагрузках, но усиленный наплыв приводит к чрезмерному расходу электродного металла и в связи с этим для его использования нужно экономическое обоснование.
- Вогнутые (ослабленные) способы используются для скрепления тонкого металла.
- Нормальные или плоские актуальны при динамических нагрузках, так как они не имеют особого перепада между дорожкой и основным металлом.
По виду сварки
Классификация сварных швов по виду сварки разделяется в зависимости от типа воздействия сварочного аппарата. Например, при работе в среде аргона или другого защитного газа, соединение будет не иначе, как «газовым», при работе с электродом – «электродуговым». Самыми основными видами являются следующие швы:
- ручной дуговой сварки – стыковое или нахлесточное соединение реализуется вручную с помощью электрода. Таким образом, можно скрепить практически любой металл, толщиной от 0,1 до 100 мм в любом положении;
- автоматической сварки, которые осуществляются при работе с аппаратом – трансформатором, выпрямителем или инвертором;
- сварки в инертном газе. Такие стыковые, угловые и нахлесточные соединения считаются самые прочные, так как сварка происходит в среде инертных газов, которые защищают его от окисления. Большим плюсом такого скрепления является эстетический вид и отсутствие отходов и шлаков;
- газовой сварки – дорожка формируется под воздействием температуры, которая создается за счет горения рабочего газа, исходящего из горелки;
- паяных соединений, которые совершаются с помощью паяльника.
Кроме описанных, существует еще множество способов для соединения деталей, как обычных, так и нестандартных, которые применяются для заваривания деталей в труднодоступных местах. Например, швы могут быть однослойными (а) или многослойными(б, в), при которых накладывается несколько валиков, располагающихся на одном уровне поперечного сечения шва.
svarkaed.ru
типы и устройство :: SYL.ru
Любые конструкции и строения подвергаются деформации по разным причинам: оседание здания после строительства в процессе эксплуатации, температурные и сейсмические воздействия, неоднородность грунтов в основании конструкций. Несомненно, при проектировании и строительстве необходимо учитывать все эти факторы и сделать объект максимально безопасным для людей, а также минимизировать возможность повреждений и риск частого ремонта. Поскольку в современном мире все чаще строят большие и массивные сооружения как жилые, так и торговые, промышленные, невозможно обойтись без применения деформационных швов во всех конструктивных элементах строений.
Определение, назначение деформационных швов
С целью уменьшения напряжения в конструкциях из-за деформации и усадки элементов зданий, мостов, дорог и других сооружений в них устраивают деформационные швы. Это элементы, разделяющие все строение на отдельные блоки, что позволяет им свободно двигаться в определенных направлениях. Данное явление значительно снижает риск разрушения конструкций в местах возможной деформации. Участки, разделенные подобными швами, оседают равномерно внутри своего объема, не мешая целостности соседних блоков.
Виды деформационных швов
Существует множество классификаций деформационных швов.
Типы деформационных швов по характеру нагрузки, из-за которой возникает деформация:
- Осадочные. Данные деформации возникают из-за неравномерного уплотнения грунтов под разными частями здания. Это может происходить по нескольким причинам. Во-первых, на изменения влияет неравномерное распределение веса. В современной архитектуре часто строят дома с разной этажностью, с многими конструктивными особенностями в частях здания. Во-вторых, причиной может служить разнородность грунтов под отдельными частями сооружения или дома. Однородный грунт под всем основанием считается идеальным случаем, который встречается крайне редко. При значительной разнице величин осадки отдельных элементов могут возникать вертикальные деформации в виде изломов, сдвигов, трещин, смещений. Деформационные швы осадочного типа рассчитывают для каждого случая отдельно и устраивают вертикально по всей высоте здания от фундамента. Они призваны компенсировать разницу между осадкой отдельных конструктивных блоков.
- Усадочные. Такие деформации вызваны уменьшением объема конструкций и элементов. Этому явлению подвержены все бетонные монолитные части и каменная кладка: при застывании и твердении смесь теряет влагу. Данный аспект также рассчитывается, и конструкцию делят на определенные части для избегания трещин, надломов и пр.
- Температурные. Особенно важно учитывать данный тип деформации в местности со сменой климата: лето-зима. В разное время года конструкции наружных частей подвергаются воздействиям температур, что сказывается на их объеме. Особенно в зимний период, когда стена с внутренней стороны помещения и с улицы имеет существенную разницу температур. При том, что внутренняя часть ее имеет постоянную температуру, а наружная подвергается большим изменениям, внутри конструкции может возникать внутреннее напряжение, способное достичь предела и привести к необратимым последствиям. Для решения данной проблемы устраивают температурные швы. Часто они совпадают с усадочными. В отличии от осадочных, температурные швы необходимы только в наземной части зданий, поскольку фундамент не испытывает больших колебаний температур, если рассчитан и устроен верно.
- Сейсмические нагрузки возникают в районах с частыми землетрясениями и колебаниями почвы. В этих случаях здания особым образом делят на отдельные самостоятельные блоки, разделяемые специальными сейсмическими деформационными швами, имеющими особое строение, что позволяет сохранить целостность конструкций при сейсмической активности.
Помимо этого, деформационные швы в зданиях классифицируют по типу конструкции, в которой они устроены. Выделяют швы, находящиеся:
- в стенах;
- в фундаментах;
- в бетонных полах;
- в монолитных плитах.
Деформационный шов в каждом элементе имеет отдельное строение. Таким образом учитываются особенности изменений форм и нагрузок для каждого участка и направления. К этой классификации дополнительно можно отнести деформационный шов между зданиями. Например, в городском пространстве часто можно встретить сопряженные между собой жилые дома и магазины. Они, как правило, имеют разные архитектурные особенности, объемы и размеры, материалы строительства, но их объединяет одна общая стена. Чтобы эти объекты не влияли на изменения друг друга, между ними также устраивают компенсирующие швы.
Проектирование: основные нюансы
При проектировании строений учитывают все возможные нагрузки, которые будут воздействовать на конструктивные элементы, и в зависимости от этого распределяют деформационные швы таким образом, чтобы они компенсировали все разрушающие эффекты, направленные на каждый элемент.
Устройство деформационных швов разнообразно. Их производят на строительной площадке из специальных материалов или набирающих популярность готовых металлических профилей. Конструкция деформационного шва из металла включает в себя специальный прокат и (при необходимости) вставки из различных материалов, подобранных в зависимости от места применения. Для каждого элемента здания направляющие имеют различное строение и готовятся из несхожих материалов, поскольку выполняют они разные функции.
На стадии проектирования рассчитывают не только места расположения компенсирующих разрезов, их частоту, размер и состав. Часто для отдельных мест определяют отличный от других деформационный шов. Узел, отображающий принцип примыкания конструкций, должен быть прорисован и расписан подробно, чтобы на строительной площадке не возникло трудностей с его сборкой. В каждом случае состав и вид шва могут быть индивидуальны, поскольку разные части конструкций испытывают определенные нагрузки, не всегда одинаковые. Такие ситуации могут возникнуть в местах сопряжений блоков разной этажности, назначения, веса и т.д.
Компенсационный шов в разных элементах здания
Для всех конструкций устройство компенсирующих зазоров индивидуально, они имеют собственное техническое решение, состав, размеры и особенности. Каждому материалу и конструкции соответствует свой деформационный шов. СНиП 2.03.04-84 приводит пример расчетов для наиболее распространенных железобетонных конструкций в различных условиях, СНиП 2.01.09-91 рассказывает о расчетах в просадочных грунтах и подрабатываемых территориях.
Швы в фундаментах: назначение
Фундамент – одна из самых сложных и ответственных в возведении частей любого строения. От его целостности зависят безопасное функционирование и надежность сооружения. Поэтому в его конструкции все должно быть продумано до мелочей – от правильного конструктивного решения до верно устроенных деформационных швов. Фундамент испытывает сразу несколько видов разрушающих нагрузок: от усадки и сезонного движения грунта; неравномерного оседания разных частей здания. Наружный периметр может быть подвержен температурным перепадам (в редких случаях, чаще говорится о верхней части стены фундамента, переходящей в цоколь). Деформационный шов в фундаментах должен компенсировать все поступающие воздействия и придавать ему упругости и подвижности. Кроме того, он должен иметь качественную внешнюю гидроизоляцию, которая предотвратит проникновение влаги в тело шва для избегания разрушения самого его основания.
Особенности устройства
Деформационный шов в фундаментах устраивают по всей высоте его стены от подошвы основания. Расстояние между швами определяется расчетом и зависит от величины влияющих нагрузок, типа грунтов, материала для стен, функционального назначения помещений и т.д. Для кирпичных строений шаг составляет от 15 до 30 м, для деревянных – до 70 м. Кроме этого, на границах частей здания, имеющих разное техническое назначение, также должны присутствовать компенсирующие разрывы, поскольку там возникает наибольшее напряжение.
Деформационный шов в плите фундамента представляет собой зазор, разделяющий ее на отдельные блоки. Его заполняют паклей, пропитанной смолой.
Одной из составляющих фундамента является отмостка. Она также нуждается в компенсирующих разрывах, ведь при неровном ее оседании и движении грунтов данный элемент может попросту надломиться, что повлечет за собой намокание стен основания. Отмостка перестанет выполнять свою защитную функцию. Швы устраиваются с шагом до 2 метров, в них укладывают деревянные рейки и сверху заливают горячим битумом или другим полимером, обеспечивающим надежную гидроизоляцию.
Место стыка отмостки и фундаментной стены обязательно имеет подвижный шов. Обычно его роль играет гидроизоляционная отделка наружной стены основания.
Деформационные швы в стене
Вертикальные конструкции подвержены воздействию сразу нескольких деформационных нагрузок. На них влияют осадка в процессе эксплуатации, температурные воздействия (сезонные и с одновременным перепадом температур наружной и внутренней части в холодное время), нагрузка от верхнего покрытия, снеговые массы. Потому, рассчитывая деформационный шов в стене при проектировании, важно учесть все воздействия и устроить разделения, которые не дадут конструкции разрушиться.
В современном строительстве используют самые разнообразные материалы и методы для возведения стен, которые бывают:
- сборными блочными и кирпичными;
- монолитными бетонными/железобетонными;
- сборными панельными;
- комбинированными.
Во всех из них возникают разрушающие воздействия, причем чем прочнее и тверже материал, тем большие деформационные нагрузки возникают в конструкции. Деление стены на блоки с помощью компенсационных швов позволяет отдельным частям деформироваться в определенных интервалах без угрозы разрушения всего элемента, внутри которого не возникает опасное напряжение.
Проектирование и устройство деформационных швов в вертикальных конструкциях
Для внутренних и наружных стен шаг разрывов рассчитывается по-разному, делается это на стадии проектирования. Высоту стен разделяют на отсеки по всей высоте, устраивая между ними деформационные швы. Расстояние между ними для несущих стен после расчетов - от 20 м, для внутренних перегородок – до 30 м. Расположение деформационных швов в местах максимальных напряжений позволяет снимать эти самые напряжения. Как говорилось ранее, температурные и усадочные швы возникают в надземной части дома и в основном совпадают, располагаются в местах наибольшей концентрации перепадов температур – у углов наружных стен. Деформационные швы, компенсирующие осадочные воздействия, устраиваются по всей высоте стены до основания фундамента и равномерно распределяются по длине здания.
Важным нюансом проектирования швов в стенах является их заполнение и оформление, поскольку находятся они на видимых частях любого строения, особенно, если не подразумевается дополнительная облицовка.
Температурные деформационные швы устраивают в горизонтальной плоскости стены. В процессе возведения в кладке размещают шпунт, который обкладывают толем в 2 слоя и забивают паклей. Закрывают шов глиняным замком. Данные материалы не реагируют на перепады температур, тем самым компенсируют деформацию стены. При ручной кладке заделка получается незаметной и не требует дополнительной облицовки.
В современном строительстве все чаще применяют профили для деформационных швов. Достоинством применения их является особая конструкция, армирующая зазор в стене. Это предотвращает появление трещин в области деформационного шва в процессе воздействия разрушающих нагрузок. Кроме этого, в теле профиля имеются вставки из гидрофобных материалов, что предотвращает попадание влаги в стеновой материал и дальнейшее его разрушение. Оформление наружной части деформационного шва выполнено таким образом, что он отлично вписывается в любой фасад. Большой ассортимент предлагаемых профилей позволяет подобрать к любому зданию наиболее подходящий дизайн.
Швы в горизонтальных плитах
При устройстве монолитных плит перекрытий обязательно должны быть выполнены деформационные швы, поскольку бетон является жестким неэластичным материалом и подвержен разрушению в результате воздействия различных нагрузок и одновременного оседания всего объема здания. С помощью расчетов определяют ширину одного блока перекрытия, и по такому параметру производят заливку межэтажных элементов. Заполнение швов выполняют с использованием гидроизолирующих материалов и заделок.
Швы в бетонных полах
Полы постоянно принимают нагрузку от предметов интерьера, оборудования, а их покрытия все время подвергаются износу. В одном помещении могут быть устроены полы из разных материалов, которые в процессе эксплуатации непохоже реагируют на поступающую нагрузку, влажность и другие воздействия. Такие участки тоже нуждаются в разделении, как и монолитный бетонный пол.
По назначению деформационные швы в бетонных полах разделяют на 3 основных типа.
- Изоляционный шов имеет круглую или квадратную форму, отделяет пол от стен, колонн и других внутренних вертикальных конструкций, от их воздействия во избежание деформации напольного покрытия. При его устройстве весь периметр прокладывают полимерной изоляцией и внутри образовавшегося контура производят заливку бетонного пола.
- Усадочный шов предназначен для предотвращения растрескивания бетона во время застывания и эксплуатации. Его устраивают двумя способами: при помощи формующих швы реек, которые вставляют в материал до потери им пластичности; нарезкой и устройством после окончательной обработки поверхности.
- Конструкционный шов выполняют на границах смен заливки участков полов. Он имеет сложный вид соединения "шип-паз" и позволяет бетону двигаться в горизонтальной плоскости и не допускает изменения соседних участков.
Деформационные швы в полах представляют собой зазоры, разделяющие поверхность на несколько блоков или участков. В подавляющем большинстве для устройства компенсационных швов применяют различные профильные конструкции.
Основные виды профилей для устройства швов в полах выделяют следующие.
- Встроенные – системы из алюминия, встраиваемые в плоскость напольного покрытия. Применяются в сухих промышленных помещениях с высокой проходимостью, подвергающихся регулярным воздействиям тяжелого оборудования, машин и спецтехники. Профиль может быть усилен резиновой вставкой, может иметь декоративную накладку из нержавеющей стали.
- Накладные. Данные системы устанавливают на стыке разных покрытий. Они представляют собой накладку на шов. Такие профили также выдерживают интенсивные нагрузки от техники и большого количества людей. При повышенной загруженности профиль может быть усилен полимерными вставками.
- Водонепроницаемые системы профилей предназначены не только для компенсации деформационных нагрузок, но и для защиты напольного разреза от попадания влаги и воды в помещениях с малой гидроизоляцией или на открытых площадках, парковках, складах и т.д. Такие профили выполнены из нержавеющей стали, имеют в своей конструкции специальные прокладки из ПВХ или резины.
- Разделительные системы представляют собой профили из мягкого или жесткого ПВХ. Их устраивают в качестве температурных и компенсирующих швов в монолитных полах различного назначения. ПВХ-профили герметизируют и защищают напольные стыки, они стойки к воздействию температур, кислот и моющих средств, что делает их применение универсальным. Деформационные швы в бетонных полах иногда заполняют полимерными мастиками. ПВХ-системы наиболее функциональны и долговечны, поэтому следует отдать им предпочтение.
Технология устройства разделительных швов в полах
Бетонные полы заливают не за один раз всю площадь, а частями, в несколько этапов. Разделительные швы необходимо устраивать в местах стыков разных участков заливки, поскольку бетон может иметь отличающиеся свойства. Зачастую перед заливными работами периметр участка ограничивают изолирующими материалами, которые впоследствии будут служить в качестве заделки образовавшихся стыков. Если площадь заливки большая, то швы можно нарезать уже в готовых полах. Размер зазоров и расстояние между ними рассчитывают, исходя из размера коэффициента линейного расширения бетона. Средняя ширина шва 12-20 мм, расстояние между разрезами – 1,5 м. Глубина достигает 2-3 см. Разделение производят с помощью специального оборудования. Нарезанные по готовому полу швы заполняют специальными уплотнителями и герметизируют их износостойкими полимерами или встраивают в них специализированные профили.
Швы на стыках зданий
Нередко к существующим зданиям пристраивают дополнительные: в виду экономии места в пределах города или удобства пользования в частном порядке. Пристрои могут иметь различное назначение: торговые площади, офисные помещения, бани, гаражи, хозяйственные постройки. Почти всегда осадка основного и дополнительного строений происходит по-разному. Чтобы избежать связанных с этим явлением неприятностей, нужно устраивать деформационный шов между зданиями.
Зазоры между зданиями компенсируют все виды воздействий: осадочные, усадочные, температурные, сейсмические. Поскольку основное и пристраиваемое здания имеют одну общую стену, в ней организовывают компенсационный шов, объединяющий функцию защиты от всех поступающих нагрузок.
Также прокладка между стенами нужна при неоднородности материала: например, первоначальное строение каменное, а дополнительное – деревянное. В этом случае шов может быть выполнен из гидроизоляционного материала без дополнительных конструкций.
Если фундамент под пристрой не был рассчитан сразу, а возводится дополнительно, обязательно нужно отделить его от основного с помощью шва, ведь его конструкция может отличаться. В этом случае будет происходить усадка и осадка самого основания и опираемого строения.
Компенсационный шов устраивают по всей высоте примыкающего здания.
www.syl.ru
Виды сварочных швов: характеризующие признаки
Решившись научиться искусству сваривания металла, жаждущий знаний обращается в учебную организацию, которая по истечении некоторого времени научит молодого специалиста всем тонкостям работы. Главное понять, какими бывают виды сварочных швов для успешного применения их на практике. Качественное учение рассчитано не на один год и после окончания срока начинающему сварщику, конечно, после прохождения практики присваивается квалификация или разряд, который он может по желанию повысить. На сегодняшний день высоким показателем мастерства сварки становится собственное клеймо, которое профессионал ставит на изделия, над которыми работал.

Качественно выполненные сварочные швы позволят прослужить изделиям очень долго.
Итак, прежде всего следует разделить основные понятия: сварочный шов и соединение. Они различны не принципиально, но отдельные моменты все же присутствуют.
- Шов — это непосредственно место, где происходит расплавление и кристаллизация металла в изделии. Зависит от мастерства, оборудования и особенностей металла.
- Соединение же включает в себя и шов, и прилегающие зоны, участвующие либо нет в процессе сварки. Характеризуется процессами, позволяющими оценить качество работы по окончании процесса.
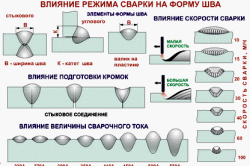
Влияние режима сварки на форму шва.
Важно отделять их как понятия друг от друга, так как качество шва определяется первым и, наоборот, качественная работа зависит от характера шва. Эти определения никогда не будут в раздельности, но сами по себе представляют отличные свойства и характеристики для того или иного вида сварочного соединения.
Швы классифицируются по многим признакам. По поперечному сечению:
- Стыковые.
- Угловые.
- Прорезные.
Более подробно о классификации
Самые распространенные виды соединения — стыковые. Шов в таком случае используется один. Плюсовыми качествами шов обладает на предмет деформации — он может ей подвергнуться лишь при значительных и намеренных нагрузках. Так как подготовка металла и выбор электродов в шве происходит тщательно, то в качестве можно быть уверенным.
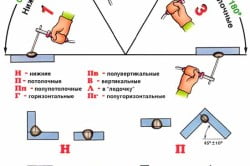
Классификация и обозначение сварочных швов.
В угловых соединения шов может располагаться под любым углом, но при этом учитывается толщина металла — не более 3 мм, ибо напряжение все же присутствует.
Прорезные или нахлесточные соединения предполагают большой расход материала, но не требуют его тщательной обработки. Как правило, при таких соединениях используется двойной шов, чтобы не допустить негерметичности.
Есть еще тавровые соединения, при которых швы представляют собой двойные, по местам стыка в форме буквы Т. Их используют в работе над несущими конструкциями и сварка в этом случае становится важнейшим моментом.
Прежде чем начинать работу, нужно определиться, какие виды швов подойдут именно данному изделию. Отличием может служить его конфигурация и протяженность:
Конфигурация:
- Прямая.
- Кривая.
- Окружная.
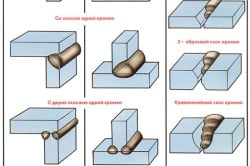
Основные типы сварочных соединений.
Прямолинейная сварка подразумевает под собой соединение деталей, соответствующих размеру изделия по одной линии. Этому подлежат профильные и направляющие конструкции.
- Кривая сварка. Это означает, что соединение конструкций может быть разных форм. К примеру, круглой трубы и профиля.
- Круговая сварка относится к швам, соединяющим полые трубы или другие круговидные предметы различного диаметра.
Дополнительные характеризующие признаки
Виды швов делятся по протяженности, что тоже имеет смысл в категории работ:
- Сплошные — короткие, средние и длинные.
- Прерывистые — прихваточные и конструкционные.
Размеры сварки швов определяются необходимостью работы над определенными конструкциями, которые бывают различными в размерах. Короткие размеры шва равны 300 мм, средние и длинные до 1 м и более. Они хороши, когда конструкции прямолинейные и длинные, к примеру, магистрали.
Прихваточные швы могут быть как временные, так и монолитные, где удержание конструкции будет определяющим фактором. Расположение их разное: по одной стороне или на двух в шахматном порядке. С их помощью варятся каркасы, стойки, секции и прочее.
По количеству накладок виды швов могут быть:
- Односторонние.
- Двусторонние.
- Многослойные.
Любое количество накладок определяется необходимостью.
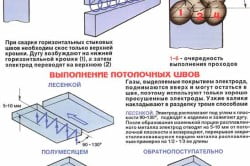
Выполнение горизонтальных швов.
Изделия, подвергающиеся сварке, требуют наличие хотя бы минимальной жесткости и напряжения, иначе их можно было соединить чем-то менее прочным. Если большего не требуется, то обходятся минимальным числом сварочных швов.
Двойные варианты уже подразумевают более прочную конструкцию. В них не допускается негерметичность.
Накладка нескольких швов предполагает сварку ответственных конструкций, где усиление элементов играет важную роль. Таким образом происходит сварка толстостенных металлов, дабы избежать расхождения при напряжениях.
Какие еще бывают швы: особенности
Швы бывают:
- Нормальные.
- Выпуклые.
- Вогнутые.
Чтобы выполнить все указанные виды, мастерство сварщика должно быть на высоте, потому что такие швы используются для конструкций неправильных форм, значит, в сложных геометрических деталях. Выпуклые и вогнутые швы допускаются для соединения декоративных форм либо там, где другой шов прямолинейный положен быть не может. Отбивая шлак от такого вида шва, сварщику требуется умение и осторожность, так как есть риск испортить конструкцию.
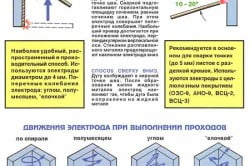
Выполнение вертикальных швов.
Расположение в пространстве также влияет на вид используемого шва, ибо уже не получится повернуть к себе конструкцию удобным боком. Таким образом, все решает его вид, который будет наложен на:
- Нижние конструкции.
- Потолочные.
- Горизонтальные.
- Вертикальные.
Кладутся они на соответствующих поверхностях и могут иметь некоторые различия. К примеру, выполняя потолочную сварку, имеет смысл применять нахлесточные швы, так как поверхность расположена таким образом, что металл способен стекать и образовывать непровары, и соединение надежным не будет.
Швы не являются самыми надежными соединениями, поэтому по их прокладке нужны большие знания, чтобы избежать распространенных повреждений при работе:
- Подрезы.
- Непровары.
- Шлаковые вкрапления.
- Поры.
- Горячие трещины.
- Полости.
- Несплавления.
- Прожоги.
Подрезы — повреждения, которые получаются вдоль шва из-за неправильных механических действий. Сварочный аппарат обладает мощностью, поэтому прикосновение дуги к местам, для этого не предназначенным, чревато образованными разрезами. Кроме того, сварочные подрезы могут быть вызваны большим количеством брызг раскаленного металла, если заранее не отрегулировать агрегат или пользоваться отсыревшими электродами.
Непровары — шов без соединения с металлом. Если оставить это без внимания, то впоследствии на этих местах образуется ржавчина и шлак. Это приведет к разрушениям впоследствии и к тратам, так как либо придется варить конструкцию по-новому, либо менять ее.
Шлаковый вид повреждений шва может получиться из-за некачественных электродов и неквалифицированной работы мастера. Если не убрать их сразу, приставания их в горячем виде неизбежно, а отбивание чревато повреждениями.
Поры — еще один вид порчи сварки. Это мелкие крапинки или даже дырочки, образованные от летящих брызг расплавленного металла. Чтобы такого не произошло, осуществляют манипуляции с током сварочного аппарата: уменьшают или меняют частоту, меняют вид самой сварки.
Горячие трещины образуются непосредственно от неправильно подобранного материала, при котором точки плавления различны, один из них может дать трещину. Сварка не самая простая специальность, нужно знать, какие материалы лучше всего соотносятся с другими. Швов и соединений может быть множество. Трещины являются самыми опасными дефектами плохой сварки и могут вызвать разрушения большого масштаба. Практически всегда мгновенны, что позволяет сразу обнаружить неисправность.
Полости швов опасны тем, что сразу обнаружить их не удается. Металл сваривается пузырем, и внутри него скапливаются газы, способные расширятся или нагреваться при перепадах температур. В итоге соединение треснет.
Несплавления представляют собой пустые места без валика в наплавках. Чреваты непроварами, что напрочь снижает качество соединений и швов, значит, грозит неустойчивостью. Стоит иметь это в виду и по окончании сварки пройтись по поверхности визуально.
Прожоги происходят из-за попадания раскаленного металла на поверхность. Это чаще всего встречается в виде потолочного сваривания или вертикального. Чтобы этого избежать нужно изучить возможности своего сварочного аппарата, характеристики сталей и электродов — не всеми можно сваривать разные изделия. Пренебрегая этим, нельзя добиться качественных соединений и швов.
Заключение и подведение итогов
Таким образом, рассмотрев неполный перечень дефектов швов, можно понять, каким образом их избежать и сделать соединение качественным. Есть несколько способов обнаружить недостатки, сделанные сварочным швом:
- Визуальным осмотром.
- Обмером.
- Испытанием на герметичность.
- Контрольно-измерительными приборами.
- Лабораторными опытами.
Соединение считается качественным, если:
- визуальный осмотр не выявляет никаких нарушений;
- обмер подходит под стандарт, регламентирующий необходимые цифры;
- герметичность не вызывает нареканий: вода не бежит, газ не просачивается;
- манометры и анализаторы указывают на отсутствие утечки;
- опыты веществ и металлов показывают невзаимодействующие друг с другом функции.
Если все условия соблюдены и внешний вид шва не вызывает нареканий, можно считать, что соединение выполнено качественно.
moyasvarka.ru
классификация, типы сварочных соединений, основные геометрические параметры шва
Одним из способов соединения частей материала является сварка. Метод нашел очень широкое применение в разных областях. С помощью этого относительно дешевого и вместе с тем надежного метода получают неразъемные соединения. С учетом разновидностей металлов, у каждого из которых свои особенности сваривания, различий условий проведения работ и требования к соединению, выделяют разнообразные виды сварных швов и соединений.
Зоны сварки
Зона сплавления с частично оплавленными зернами — 0,1−0,4 мм главного металла. Когда металл в этой зоне прогреется, его структура становится игольчатой с высокой хрупкостью и низкой прочностью.
Зона термического делится на четыре участка:
- I — относится к основному металлу, нагревшемуся до температуры превышающей 1100 °C. Структура этого участка крупнозернистая, а зерна в этой области приблизительно в 12 раз больше, чем стандартные. Вследствие перегрева уменьшается, вязкость, пластичность и другие механические свойства металла, и в слабейшем участке сварки часто происходит разрыв.
- II — участком является зона нормализации, в которой главный металл прогревается на 900 °C. Структура зерна тут гораздо мельче, чем в предыдущем случае. Занимает этот участок 1−4 мм.
- III — зона неполной кристаллизации, в которой главный металл прогревается до 750− 900 °C. Здесь попадаются и мелкие, и крупные зерна. Механические свойства снижаются вследствие неравномерности распределения кристаллов.
- IV — зона рекристаллизации. Прогревается до 450− 750 °C и восстанавливается форма зерен, деформированных из-за прошлых механических воздействий. Примерная ширина — 5−7 мм.
Зона главного металла начинается от участка, прогревающегося менее чем на 450 °C. Структура здесь сходна со структурой основного металла, но сталь теряет крепость за счет прогревания. По границе выделяются оксиды и нитриды, ослабляющие связь зерен. Металл в этом месте становится более прочным, однако, получает меньшую пластичность и ударную вязкость.
Классификация сварных соединений и швов
Виды швов в зависимости от признаков делятся на несколько категорий. По внешнему виду выделяются:
- Нормальные.
- Выпуклые.
- Вогнутые.
По типу сварные швы бывают одно- и двусторонними. По числу проходов — одно- и многопроходными. По числу слоев: односторонние и многослойные (при сваривании толстых металлов).
Есть также разновидности по протяженности:
- Односторонние непрерывные.
- Односторонние прерывистые.
- Двусторонние цепные.
- Двусторонние шахматные.
- Точечные швы (создаваемые контактной сваркой).
Типы швов по вектору усилия воздействия:
- Поперечный — усилие перпендикулярно шву.
- Продольный — усилие параллельно шву.
- Косой — усилие под углом.
- Комбинированный — признаки и поперечного и продольного шва.
По пространственному положению:
- полупотолочный;
- горизонтальный;
- нижний;
- вертикальный;
- полугоризонтальный;
- полувертикальный;
- потолочный;
- в лодочку.
По функциям швы делятся на следующие:
- Прочные.
- Прочно-плотные.
- Герметичные.
По ширине:
- Ниточные швы, чья ширина практически не превышает величину диаметра электрода.
- Уширенные швы делаются поперечными колебательными движениями стержня.
Особенные соединения
Стыковое. Самый распространенный вариант, представляющий обыкновенное соединение торцевых поверхностей или листов. Для их формирования требуется минимум времени и металла. Могут выполняться без скоса кромок, если листы тонкие. Для изделий толстых нужно подготавливать металла под сварку, где нужно будет скашивать кромки, чтобы увеличить глубину проварки. Актуально это при толщине от 8 мм. Если толщина будет больше 12 мм, понадобится двустороннее стыковое соединение и скашивание кромок. Чаще эти соединения выполняются в горизонтальном положении.
Тавровое. Тавровые соединения имеют Т-образную форму и бывают одно- или двусторонними. С их помощью могут соединяться изделия разной толщины. Если меньшая деталь устанавливается перпендикулярно, в процессе сварки электрод наклоняется до 60°. Для осуществления более простого варианта сварки «в лодочку» пользуются прихватками. Благодаря этому уменьшается вероятность образования подрезов. Обычно шов накладывается за проход. Сегодня выпускается много аппаратов для автоматической тавровой сварки.
Угловое. У этих соединений (под разными углами) нередко подкашиваются кромки, чтоб шов залег на требуемую глубину. Двусторонняя проварка делает соединение крепче.
Внахлест. Данным способом сваривают листы толщиной менее 1 см. Они кладутся друг на друга внахлест и провариваются с двух сторон. Между ними не должно быть влаги. Для лучшего скрепления соединение иногда варится с торца.
Геометрия шва
S — толщина заготовки.
E — ширина.
B — зазор между заготовками.
H — глубина залегания проваренного участка.
T — толщина.
Q — величина выпуклой части.
P — расчетная высота, соответствующая перпендикулярной линии из места проплавления к гипотенузе наибольшего прямого треугольника, вписанного во внешнюю часть.
A — толщина углового шва, куда входит величина выпуклости и расчетной высоты.
K — катет представляет собой расстояние от поверхности одной заготовки до границы угла другой.
Q — выпуклость наплавленного участка.
Выбор
Виды швов и сварных соединений отличаются по свойствам, и для каждого случая подбираются параметры удачного сочетания. Первым делом оценивается пространственное положение. Чем легче идет работа, тем лучшим получается качество. Легче сделать горизонтальные швы, поэтому заготовки стараются выставить именно горизонтально. Иногда, для обеспечения качества деталь приходится переворачивать неоднократно.
Сваривание за проход помогает добиться лучшей крепости, чем в случае многократных проходов. Так что, требуется баланс между удобством и числом проходов.
Когда заготовки толстые, кромки разделываются, а поверхность обрабатывается для добавления ей чистоту. Стыковые варианты наиболее простые, предпочтительнее выбирать их, так как проще обеспечивается фиксация во избежание искажений геометрии готовых деталей. Кроме выбора типа внимание обращают также на температурный режим, потому что могут сместиться зоны проварки и изделие не доварится или переплавится.
tokar.guru
Типы швов и способы их изготовления
Казалось бы, что такое шов – всего лишь место скрепления двух полотен. И какая разница, каким способом шов выполнен, лишь бы он эти самые полотна удерживал. Но человечество считает по-другому и за период своей истории придумало различные виды швов, выполняющие свою основную функцию – скрепления двух полотен – с определенными особенностями. Существуют швы быстрые в исполнении, крепкие по свойствам, декоративные по назначению и так далее.
Не стало исключением и поприще полимерных пленок: на сегодняшний день известно несколько типов швов, с помощью которых можно соединить 2 куска полимерной пленки. Однако, казалось бы, столь радостная перспектива выбора шва, омрачается тесной привязанностью сварных швов к виду упаковочной пленки и способу (методу) ее сварки (пайки). К примеру, полиэтиленовую пленку проблематично, если не сказать бессмысленно, спаивать методом постоянного нагрева, в результате, приходится выбирать швы, приемлемые для импульсного нагрева. А таковых можно насчитать всего три.
Итак, способ сварки путем импульсного нагрева, или как его еще называют, термоимпульсный способ, предполагает спаивание пленки путем кратковременного нагрева сварного элемента в момент прижатия его к пленке, после чего следует остывание. Данный способ оптимален, если упаковочная пленка при нагреве изменяет свою структуру, растекаясь по сварному элементу, или приобретает излишнюю эластичность – спаять такую пленку можно только путем краткого термического воздействия. Изготовить таким способом можно, как уже говорилось, всего 3 типа шва.
"Шина"
Первый тип шва среди производителей упаковочного оборудования принято называть термином «шина». Особенностями данного шва является его ширина, которая в среднем составляет около 3 мм, хотя бывают швы уже и шире. Благодаря своей ширине, данный тип шва обладает повышенными прочностными характеристиками и способен выдерживать значительные нагрузки «на разрыв». Зачастую, рвется сама пленка, а не сваренный на ней шов.
Однако, существуют и недостатки. Учитывая, что полимерная пленка, как правило, подается из рулона и шов сваривается непосредственно на полотне, возникает проблема отделения одной упаковки от другой. Другими словами, проблема разрезания пленки. В этом случае приходиться использовать ручной труд или комплектовать упаковочное оборудование механическим ножом, разрезающим пленку после сварки шва. Еще одним недостатком является длительное время сварки шва, но это общий недостаток импульсного нагрева, который характерен для всех типов швов, изготовляемых данным способом, поэтому ставить его в вину «шине» мы не будем.
Изготовляется «шина» путем использования в качестве сварного элемента тонкой, узкой и длинной полоски нихрома – нихромовой ленты или шины, откуда, собственно, и название шва. Нихромовая лента, через изолятор, натягивается на прижимном элементе паечного узла, к ней подводится питание от блока управления, контролирующего длительность и силу импульса, после чего лента покрывается тефлоновой лакотканью. Лакоткань необходима для исключения прилипания упаковочной пленки к раскаленной шине. Место опускания прижимного элемента (станина) также содержит изолятор, выполняющий, к тому же, роль уплотнителя и амортизатора, и покрыто аналогичной лакотканью.
Если между станиной и прижимным элементом поместить куски полимерной пленки и плотно прижать прижимной элемент к станине, то в момент его прижатия блок управления подаст питание на нихромовую ленту, разогревая ее и создавая эффект вскипания пленки. Через заданный интервал времени (как правило, устанавливается оператором) блок управления отключит питание и шина начнет остывать, формируя одноименный тип шва. Если в этот момент, не дав остыть шине и пленке, разжать паечный узел, можно понаблюдать эффект «съеживания» пленки в районе шва. Особенно хорошо это видно на примере полиэтиленовой пленки.
Используется в оборудовании:
• Ручной настольный запайщик импульсного нагрева Н-400, Н-600• Напольный горизонтальный запайщик импульсного нагрева ЗГИ-500, ЗГИ-700
Именно поэтому, данный тип шва предполагает кратковременный нагрев и дальнейшее остывание пленки, и именно поэтому, данный способ сварки называют термоимпульсным. Здесь важно выждать время, в течении которого шов окончательно сформируется (для облегчения данной задачи некоторые модели оборудования комплектуются таймером или индикатором остывания), что, собственно, и является ключевым недостатком импульсного способа сварки.
"Струна"
Второй тип шва называют «струна». В отличие от первого, т.е. «шины», при изготовлении «струны» паечный узел упаковочного оборудования производит сразу 2 операции: сварку и резку пленки. Соответственно, скорость изготовления упаковок на «струне» значительно выше, чем на «шине», ведь не нужно более тратить время на резку пленки. Но, опять же, есть и обратная сторона медали – шов получается очень тонким и значительно менее крепким на разрыв, нежели «шина». В этом случае, уже больше вероятности, что порвется шов, а не сама пленка.
Используется в оборудовании:
• Ручной настольный запайщик импульсного нагрева L-400x400• Напольный запайщик импульсного нагрева ЗПИ-500 ... ЗПИ-2500• Ручная термокамера ТН-1, ТН-2
Изготавливают «струну» таким же устройством, что и «шину», с той только разницей, что вместо нихромомой ленты используют нихромовую струну. Имея круглое сечение и значительно меньшую площадь, чем шина, струна фактически прожигает упаковочную пленку, одновременно оплавляя ее края. Получается проплавленное рассечение полотнища со слипшимися краями – шов типа «струна». Причем, что характерно, струна, рассекая пленку, оплавляет края по обе стороны рассечения, формируя, по сути два шва одновременно. Однако, как уже упоминалось, повышенная производительность в изготовлении швов приводит к жертвам в виде их крепости.
"Комби"
Третий тип шва возник из стремления совместить первые два, причем стремление было вызвано действительной потребностью. В частности, при упаковке пенопластовых или пенополистирольных плит натяжение пленки не позволяет эффективно использовать механический нож, а шов типа "струна" разрывается практически сразу после сваривания. Пришлось скомбинировать "шину" и "струну", условно назвав данный тип шва "комби".
Можно, конечно, возразить, что такой шов вовсе и не отдельный тип, а всего лишь сварка двух предыдущих типов, но как показала практика, не все так просто. Поначалу, мы тоже думали использовать струну исключительно как режущий инструмент, сваривая пленку только шиной. Однако в действительности получилось, что струна не просто режет пленку, но и продолжает сваривать ее, дополняя шину – шов получается не совсем «шинный» и имеет плавленый край. Детально рассмотрев его и не найдя описания в литературе, мы, не мудрствуя лукаво, решили для удобства использования и понимания о чем идет речь окрестить его «комби». Несогласные с таким подходом могут продолжать пользоваться терминами «шина»+«струна», «шина» и резка «струной» и прочими аналогичными. На наш взгляд, это не совсем удобно.
Используется в оборудовании:
• Упаковщик пенопластовых плит АУП-4
Изготавливается данный тип шва, как уже можно было догадаться, путем сочетания в паечном узле нихромой шины и нихромовой струны. В остальном, конструкция паечного узла (прижимного элемента и станины) аналогична описанной выше. Также, следует отменить, что, несмотря на, казалось бы, явные преимущества данного типа шва как перед "шиной", так и перед "струной", используется он крайне редко и, на сегодня, нам известен только один вид упаковочного оборудования применяющий его.
Собственно, на этом перечень типов швов, изготавливаемых путем импульсного нагрева, можно считать полностью исчерпанным. И если вы планируете упаковывать продукцию в полимеры, для которых применяется только импульсный нагрев (к примеру, тот же полиэтилен), выбор ваш ограничен, по сути, двумя типами швов: «шина» или «струна». Соответственно, придется чем-то пожертвовать: производительностью во благо крепости или крепостью шва во имя повышенной производительности.
Если же используемые упаковочные полимеры допускают применение не только импульсного нагрева, можно рассмотреть типы швов, изготавливаемые постоянным нагревом. Хотя их, к сожалению, тоже не очень много, а именно два.
Способ пайки пленки с помощью постоянного нагрева, как уже можно было догадаться из названия, предполагает сварку пленки с помощью сварного элемента, на котором поддерживается постоянная заданная температура. В отличие от термоимпульсного способа, при сварке постоянным нагревом не требуется остывание пленки и сварного элемента, соответственно, экономиться время, затраченное на формирования шва. В данном случае, от сварного элемента требуется лишь прижатие к упаковочной пленке на время, достаточное для сварки шва, после чего можно сразу переходить с сварке следующего шва. Изготовить таким способом можно следующие типы швов.
"Еврошов"
Данный тип шва является, пожалуй, самым прочным и эстетичным среди всех типов шва. Его ширина колеблется в пределах от 10 до 20 мм (хотя бывают и другие варианты), обеспечивая достаточно весомые показатели прочности, а использование рифленых сварных элементов делает такой тип шва привлекательным в глазах потребителя. Кроме того, учитывая способ сварки, можно утверждать, что "еврошов" является самым быстроизготавливаемым.
Однако, столь радужная ситуация омрачается невозможностью изготовить данный тип шва способом импульсного нагрева, что исключает его применение для дешевой и прочной полиэтиленововой пленки. Те же пленки, которые приемлют "постоянный нагрев", либо стоят значительно дороже полиэтилена, либо менее прочны. Таким образом, "еврошов", по большей части, выполняет функцию декоративного украшения красивой упаковки, чем функцию наиболее прочного шва.
Используется в оборудовании:
• Ручной настольный запайщик постоянного нагрева НE-300• Запайщик штуцеров "дой-пак" с накопителем ПЗШ-8• Фасовочный автомат с объемным дозатором для упаковки в стик-пакет АФ-120-Об
Изготавливается «еврошов» путем использования в качестве сварного элемента алюминиевого профиля П-образной формы. Существуют варианты использования стального профиля, но в большинстве случаев применяют все же алюминий, руководствуясь его лучшей теплопроводностью. Внутри профиля (в средине «П») размещают электрический тэн, с помощью которого нагревают профиль и поддерживают его температуру в заданных параметрах. Вершина «П» является сварной поверхностью и именно она, путем прижатия к пленке, формирует шов. В связи с тем, что упаковочные пленки, свариваемые постоянным нагревом, не имеют свойства прилипать к поверхностям, покрытие профиля лакотканью не требуется, как и не требуется покрытие ею станины паечного узла или контрприжимного элемента.
Поверхность вершины профиля, как правило, делают рифленой. Это связано не только с эстетическими предпочтениями, но и обусловлено чисто практическими соображениями: рифленая поверхность менее подвержена деформации при нагреве, имеет большую сварную площадь и позволяет плотно зажимать свариваемую пленку в паечном узле, что крайне необходимо при протяжке пленки в упаковочных автоматах.
"Термошов"
"Термошов" представляет собой тип шва, используемый исключительно для сварки термоусаживающейся полиэтиленовой пленки. Принцип его изготовления основан на градиентном оплавлении свариваемых кусков пленки. Другими словами, "термошов" представляет собой плавный переход от слегка слипшихся кусков пленки до полного спаивания в единую структуру. В итоге, шов получается достаточно крепким, но абсолютно не эстетичным, хотя для термоусаживающегося полиэтилена эстетика имеет минимальное значение.
Особенностями данного типа шва является способ его изготовления и ограниченная сфера применения. По способу изготовления, можно сказать, что мы наблюдаем исключение из общего правила. Ведь как утверждалось ранее, полиэтиленовую пленку можно спаять только методом импульсного нагрева – при постоянном она липнет к сварным элементам и «съеживается». Однако, «термошов» основан на постоянном нагреве – конструкция сварного элемента такова, что позволяет минимизировать прилипание, а «съеживание» для термоусаживающихся пленок является основным свойством. По сфере применения следует отметить, что вряд ли получится использовать сварной элемент, паяющий «термошов», для других видов пленок, а если даже и получится, то эффективность такого шва будет минимальна.
Соответственно, к преимуществам данного типа «шва» можно отнести его прочностные качества при относительно быстром способе изготовления, к недостаткам – неэстетичность и ограниченность в применении к упаковочным материалам.
Используется в оборудовании:
• Термотоннель с L-образным ручным запайщиком ТТ-15-L
Изготовляется «термошов» использованием сварного элемента полукруглой конфигурации. Сварной элемент состоит из полукруглого алюминиевого профиля, внутри которого расположен тэн, создающий необходимую температуру. Профиль покрыт тефлоновой лакотканью, препятствующей прилипанию пленки к раскаленному прижимному элементу. В верхней точке округлости профиля расположена стальная струна. Причем струна не имеет подачи питания на себя и нагревается исключительно за счет нагрева профиля. Станина паечного узла, аналогично «шине», содержит изолятор (он же – уплотнитель и амортизатор) и также покрыта лакотканью.
В момент прижатия сварного элемента к станине, пленка, за счет округлости профиля, прижимается с разным усилием и соответственно по разному оплавляется: струна прожигает пленку насквозь, выполняя роль рассекателя, а полукруг создает плавный переход от полностью сплавленных участков до слегка слипшихся, формируя градиентное оплавление.
На этом, собственно, и все - других типов швов, как и способов их изготовления, пока еще не придумано. Следовательно, выбирать приходится из того, что есть, и, как мы видим, выбор достаточно скромен. А если еще учесть, что каждый тип используемой упаковочной пленки, требует определенного способа сварки, то выбор становиться совсем мизерный. Но, все же, выбор есть, и только пользователь упаковочного оборудования может определиться, что ему, в конечном счете, важнее: прочность, скорость изготовления или привлекательность упаковки.
packtech.com.ua