Предлагает услуги по пошиву одежды оптом, а именно:
пошив униформы
пошив корпоративной одежды
пошив промо формы (промо одежды)
пошив рубашек
пошив брюк
пошив юбок
пошив форменной и фирменной одежды
пошив комбинезонов и полукомбинезонов
пошив футболок и толстовок
пошив платьев и блузок
пошив жакетов и пиджаков
пошив медицинской одежды и рабочей одежды
пошив ветровок и курток
пошив пиджаков и костюмов
пошив пальто и плащей
Как раскроить лист ДСП своими руками и с помощью распиловочного станка. Как правильно кроить плитный материал
Методы и принципы раскроя листовых материалов ОСБ, фанера, ДСП, МДФ
Как распилить ОСБ, фанеру, ДСП, МДФ без сколов
Деревосодержащие плиты используются в строительном деле как для создания несущих элементов здания, так и в качестве различных видов обшивки. Подобные материалы применяются также для сборки лестниц, дверей, корпусной мебели и прочих габаритных предметов/конструкций. В любом случае крупноформатные листы (фанеру, OSB, МДФ и ДСП) мастеру приходится кроить и подгонять прямо на объекте. О том, как это сделать быстро и качественно будет данная статья. Ниже мы рассмотрим основные приёмы резки, сделаем акцент на практические нюансы, которые будут одинаково актуальными для всех плитных материалов, произведённых методом прессования древесных волокон с добавлением клея.
Какой инструмент выбрать
Листовые материалы из древесины всегда имеют в своём составе смолы и клея, которыми шпон, щепа или опилки соединяются в единое целое. Полученные плиты из-за этого получаются плотными и упругими, с приличной долей вязкости. По многим физическим показателям они превосходят цельные хвойные пиломатериалы, но при этом и обрабатывать их немного сложнее. Между тем, любая фанера, ориентированно-стружечная плита, МДФ или ДСП – пилится, сверлится, шлифуется, фрезеруется…
Распил фанеры лобзиком
Распил фанеры дисковой пилой
Как подготовиться к раскрою листовых материалов
Ручная пила, нож. При определённом упорстве и небольшом объёме работ можно обойтись даже обычным ручным инструментом, но, как показывает практика, при таком подходе страдает не только производительность, но также и качество раскроя. Ручной ножовкой трудно выполнить ровный прямой рез. Из-за неравномерной скорости подачи инструмента и медленного неравномерного рабочего хода полотна - на плоскостях возникают сколы, избавиться от которых очень сложно. Новые обрезные кромки даже у опытных пользователей редко получаются перпендикулярными основным поверхностям листа.
Важно! Если другого варианта у вас нет, то пилу для раскроя фанеры, МДФ, ДСП, OSB следует использовать с мелкими хорошо заточенными зубьями. Вести её желательно – максимально полого.
Нож, конечно, не подходит для раскроя плит ОСП, фанеры, ДСП и МДФ, но им за несколько проходов можно разрезать ДВП. Также его используют для разметки.
Электролобзик. Лобзиком можно кроить листовые материалы по прямой линии, но это слишком долго, и не всегда качество получается удовлетворительным. Свой отпечаток накладывает небольшая скорость рабочего полотна и возвратно-поступательный тип движения узкой оснастки. Какую бы пилку вы ни использовали – всегда будет ворс и сколы на одной из сторон плиты, очень сложно им выдержать прямую линию, особенно при работе вдоль волокон далеко от края листа. Но лобзик является незаменимым инструментом, если необходимо в «домашних» условиях сделать криволинейные резы.
Важно! Для раскроя электролобзиком ОСБ, Фанеры, ДСП и подобных материалов нужно правильно выбрать пилку. Лучше всего тут подходят варианты с названием «чистый рез», у которых зубья смотрят в сторону инструмента и при работе не отталкивают лобзик от листа, а наоборот – прижимают. Многие производители выпускают специальную оснастку для столярных плит, для примера можно назвать компанию Bosch.
Фрезер ручной электрический. Этот инструмент обладает очень высокой скоростью вращения шпинделя. Его оснастка может резать деревосодержащие плиты довольно чисто, причём без потемнения древесных волокон, как от лазера. Но для этого необходимо тщательно подбирать фрезу под конкретный тип материала, а также по необходимости тонко регулировать скорость хода оснастки и подачу инструмента (обычно она выбирается в пределах 5-20 мм в секунду). В большинстве случаев рез приходится делать в 2-3 прохода и более, в зависимости от толщины плиты. Очевидно, что сфера использования ручного фрезера ограничивается криволинейным раскроем небольших деталей, изготовлением разных проёмов и отверстий, а также несквозных выборок в материале.
Дисковая пила. Так называемая «циркулярка» является самым удобным и самым производительным инструментом для раскроя листовых материалов. Прямой рез после неё получается довольно качественный, мощности мотора, как правило, хватает для пиления самых толстых плит на приличной скорости. Что особенно привлекает в дисковой пиле – это возможность получить на выходе по-настоящему прямую кромку, перпендикулярную лицевым поверхностям листов. А если поменять наклон площадки – то можно изготовить кромку под 45 градусов.
Важно! Наилучших результатов в пилении столярных плит циркуляркой можно достичь, если применять диски с большим количеством зубьев. К примеру, для быстрого не слишком требовательного к чистоте раскроя лучше купить круг с 48-ю зубьями, имеющими твердосплавные напайки. Такой вариант хорош как для обычного материала, так и для ламинированного (фанера, МДФ). А для особо важных и точных работ как нельзя лучше подойдёт тонкий стальной диск со без напаек, который хоть и тупится быстрее, но меньше всего рвёт и поднимает волокна.
Ориентированно-стружечная плита, МДФ, фанера, ДСП – все эти плиты имеют довольно большие габариты, поэтому резать их чаще всего предпочитают на полу, используя возможность буквально зайти на заготовку сверху.
При больших объёмах работ, лучше, конечно, собрать для этого деревянные подмости, например, из бруска или обрезной доски второго/первого сорта. Затраченное время обязательно окупится за счёт удобства, безопасности и качества – проверено не единожды.
Какой бы инструмент ни был выбран для резки, плиту необходимо приподнять над основанием. Для этого стоит использовать деревянные бруски толщиной 40-50 мм, которые при попадании на них рабочего полотна инструмента, не нанесут вред режущим кромкам оснастки. При работе с лобзиком или ручной ножовкой бруски располагают вдоль реза, а при использовании циркулярки обычно кладут их поперёк (диск немного прорезает брусок-подкладку во время прохода).
Распил фанеры на полу
Распил фанеры на столе
Проффесиональная направляющая Фестул
Упор для лобзика из штукатурного правила
Есть три главные задачи мастера при предварительной фиксации листа.
- Избежать лишних вибраций.
- Полностью исключить возможность заклинивания оснастки в материале по мере раскроя.
- Не дать плите сломаться под своим весом, когда большая часть реза уже выполнена.
Основные проблемы решаются достаточным количеством и продуманным расположением удерживающих брусков-подкладок.
Важно! Идеальный вариант при раскрое крупноформатных листов – это когда удаётся создать «полную поддержку», то есть все детали остаются на своём месте после раскроя, а не прогибаются и не отламываются.
Есть мнение, что лист на рабочий стол нужно укладывать лицевой (которая для вас более важная) стороной вниз. Дескать, оснастка лобзика или циркулярки на выходе из материала рвёт волокна значительно больше. Однако визуально контролировать тыльную строну плиты во время реза невозможно, и так как оснастку часто немного уводит в сторону внизу - решение это можно назвать спорным.
Защитить лицевую поверхность от сколов или поднятия ворса нужно правильным выбором оснастки и рабочих режимов. Также хорошо помогает получить чистый рез наклеивание малярного скотча по линии реза (разметка производится прямо поверх бумаги).
Важно! Все лобзики и циркулярки оборудованы металлической опорной площадкой. Иногда площадка укомплектована защитной полимерной накладкой, а иногда она не имеет таковой. Чтобы от площадки на поверхности листа не оставалось царапин или чёрных следов – её также стоит оклеить малярным скотчем. Это особенно актуально при работе с ламинированными материалами, которые впоследствии не планируется шлифовать.
Разметка листовых материалов типа фанеры, ОСБ или ДСП выполняется обычно строительным карандашом или тонким маркером по линейке, которой может выступать длинный реечный уровень или штукатурное правило. Также длинные листы для кроя удобно размечать при помощи малярного отбивочного шнура.
Важно! Некоторые мастера предпочитают делать разметку, прочерчивая линию острым «сапожным» ножом. Благодаря тому, что лезвие клинка слегка прорезает волокна верхних слоёв (щепа ОСП, шпон фанеры, ламинат МДФ), заметно снижается вероятность появления сколов.
Чтобы получить чёткую прямую линию реза, есть смысл воспользоваться «направляющей». Это может быть строганная обрезная доска, брусок, обрезок раскраиваемого плитного материала с ровным заводским краем, либо алюминиевое правило. Направляющая закрепляется на плите либо саморезами, либо струбцинами. Во время раскроя опорная платформа лобзика или дисковой пилы ведётся с постоянным касанием к направляющей. Впрочем, есть для фирменных циркулярок и специальные направляющие из металла.
Вылет пилы на ползуба - чистый рез
Металлическая шина - направляющая
Направляющая из строганной доски
Некоторые практические советы по порезке листовых материалов
- 1. Старайтесь использовать максимально возможную скорость вращения оснастки. Уменьшайте её, если пила идёт с усилием, или если заготовка «подгорает». Чем выше скорость – тем меньше будет сколов.
- 2. Скорость поступательной подачи инструмента - напротив, должна быть самой маленькой.
- 3. Всегда делайте пробный рез на ненужных кусках материала. Посмотрите, насколько видна разметка при работе, подберите оптимальную скорость движения оснастки и скорость подачи инструмента, оцените качество раскроя и точность размера готовой детали.
- 4. Ведите инструмент плавно и непрерывно. Остановки обычно оставляют следы, тем более не стоит дорезать лист с двух сторон, как это делают, чтобы избежать скола в конце. Озаботьтесь, чтобы у вас был доступ ко всей разметке, положите поудобнее сетевой кабель пилы/лобзика.
- 5. Пилите не по линии, а как бы рядом с линией разметки – чтобы часть её оставалось.
- 6. При разметке и резке учитывайте толщину пропила, который формируется после прохода зубьев.
- 7. Используя циркулярку, выставляйте глубину пропила в зависимости от толщины раскраиваемой заготовки. Максимальный вылет не нужен, наиболее чистое и эффективное пиление получается, если зубья выходят за лист где-то наполовину своей длины.
- 8. Обязательно перед началом пиления убедитесь, что оснастка (диск пилы или пилка лобзика) набрала полную скорость. Иначе возможен так называемый «обратный удар».
- 9. После завершения раскроя обязательно дайте диску полностью остановиться - и только затем вынимайте оснастку из листа.
elka-palka.ru
Раскрой ДСП - способы и технология
Мебельная промышленность использует ДСП в огромных количествах. Большей частью идут в ход листы с ламинированным покрытием разных цветов и фактур. При этом самое главное в работе любого изготовителя – правильный раскрой.[contents]
ДСП и ЛДСП продается стандартными панелями следующих размеров (используемых именно в производстве мебели):
- Ширина и длина: 1,75х3,5; 1,83х2,44; 1,83х2,62; 1,83х2,75; 2,44х5,5 м.
- Толщина 10, 16, 18 и 25 мм.
Разработанный проект мебели включает деталировку, т.е. вид, количество и размер деталей, нужных для сборки. Сотрудники мастерской составляют «выкройки» — карту распила листа на нужные детали таким образом, чтобы минимизировать количество отходов. Для облегчения процесса существуют специально разработанные программы, работающие с любыми листовыми или рулонными материалами. Бывают платные (Базис-Мебельщик, bCut, Астра), в том числе работающие он-лайн, и бесплатные (Раскрой Кузнецова, Мастер).

Карту раскроя размечают на подготовленной плите или программируют на сложных станках. При этом мастер должен следить за тем, чтобы распил проводился исключительно точно, срез ровный, без сколов и дефектов.
Таким образом, раскрой ДСП – это процесс, включающий этапы:
- Разработка оптимальной схемы распила листа с минимумом остатков;
- Непосредственно распил материала, желательно с ювелирной точностью и идеальным срезом.
Что требуется для проведения раскроя
Раскроечный процесс требует вдумчивого подхода. Для его правильного проведения понадобятся:
- плоскость, совпадающая по величине с размерами плиты;
- инструмент для разметки;
- форматно-раскроечное оборудование.
Раскрой проводится на ровной твердой поверхности, при этом лист должен быть жестко зафиксирован.
При помощи специальных агрегатов осуществляются прямолинейный и криволинейный распилы. В первом случае получаются прямоугольные детали, во втором – элементы с гнутыми формами. Реже применяют смешанный распил.

Как раскроить ДСП самостоятельно
Профессиональное оборудование для разметки и распила довольно дорогостоящее, предназначено для работы с большими объемами. Поэтому приобретать их для домашнего пользования весьма накладно. Проблема раскроя имеет 2 решения: осуществить всю работу своими руками или обратиться в мебельный цех.
Для первого варианта потребуются:
- Просторное помещение: гараж, сарай. Так как процесс довольно пыльный и шумный, в квартире проводить раскрой нежелательно;
- Раскроечный рабочий стол больших размеров или несколько небольших с устойчивыми ножками и ровной поверхностью;
- Разметочные приспособления: линейки пластиковые, металлические, рулетки, направляющая рейка или шина для циркулярной пилы, маркеры водорастворимые или карандаш;
- Фиксаторы: струбцины, упоры или просто тяжелые предметы, с помощью которых можно зафиксировать плиту в одном положении;
- Инструмент для пиления: циркулярная пила с диском для дерева и его производных, ручная пила с мелким зубом, ножовка по металлу, электрический лобзик или другой ручной инструмент;
- Шлифовочный инструмент: дрель с насадкой, рубанок, наждачная бумага, напильник и т. п.
В домашних условиях добиться идеально ровного среза для ЛДСП без сколов очень сложно. Поэтому желательно сначала провести пробную распиловку на небольшом куске 16 мм ДСП.
Некоторые мастера советуют наклеить на линию распила клейкую ленту или малярный скотч. Другие рекомендуют сделать неглубокий надрез ламинированного покрытия острым ножом или пилкой, а затем уже основной лобзиком или пилой.
Если нет уверенности в своем инструменте или вышеуказанные методы не помогают избежать сколов, можно воспользоваться проверенным способом портных – разметить с небольшим припуском (до 2-4 мм) и раскроить. Лишнее снимается рубанком, дрелью с шлифнасадкой, электрофрезером с цилиндрической фрезой или напильником. В конце — довести до идеально ровного состояния мелкозернистой наждачной бумагой.
Итак, приступая к работе, начать нужно с карты раскроя. Если деталировка делается самостоятельно, без применения программ, лучше сначала вырезать «выкройки» из любого подручного материала (картон, оргалит) и найти оптимальный вариант их расположения. Зафиксировать плиту и провести тщательную разметку. Пилить нужно аккуратно, осторожно, без суеты и излишней торопливости, желательно по направляющей.
При использовании ручной пилы есть два важных условия:
- Используется инструмент с мелкими острыми зубьями.
- Держать пилу нужно под острым углом к поверхности листа.
Если используется электролобзик, его следует очень плотно прижимать к поверхности. Лучше приобрести специальные пилочки для ДСП (Makita для 16 мм ДСП, Bosh, Stayer). Неровности снимаются напильником в направлении от края к середине или шлифовальной бумагой.
Если сколов все же избежать не удалось, их легко замаскировать при помощи кромочной торцевой ленты или накладного П-образного профиля из ПВХ.
Последние несколько лет производители электроинструмента предлагают для домашнего пользования погружные циркулярные пилы серии Ламинат/ДСП с жесткими направляющими шинами, струбцинами и специальными дисками для древесно-стружечных материалов в комплекте (Festool, Virutex, Makita).

Стоимость их начинается от 15000, поэтому для разовой работы лучше обратиться в мастерскую, имеющую хотя бы один раскроечный станок.
Раскрой ДСП при помощи специального оборудования
Чтобы раскроить лист ДСП в заводских условиях, предприятия закупают специальное форматно-раскроечное оборудование.
Раскроечный станок состоит из остова, именуемого станиной, неподвижного рабочего стола, пильного узла и вспомогательных средств (упоры, линейки, дополнительные столы). Управляется через специальный блок, механический или автоматический. Принцип его действия довольно прост — имеется два диска: подрезной, надпиливающий меламиновый слой на 2-4 мм вглубь, и распилочный, на который ложится основная работа.

Выпускается 4 вида станков:
- Горизонтальные;
- Вертикальные;
- Двухсторонние;
- Раскроечные центры с числовым программным управлением (ЧПУ)
Выбор компании, которая раскроит ДСП по нужным размерам, обычно определяется близостью к месту продажи или проживания заказчика, а также отзывами других клиентов. Как правило, большинство мастерских предлагают сформировать карту по принесенному чертежу бесплатно. Далее, при помощи специальных программ проводится расчет, размечается плита и проводится непосредственный раскрой.
Срез обычно бывает ровный, не требующий дополнительной шлифовки, без заусенцев и сколов. В дополнение мастерская может предложить услуги по кромкованию и врезке фурнитуры.
drevplity.ru
5.8.3 Изготовление облицовок из шпона строганого
Строганый шпон и рулонные материалы раскраивают на гильотинных ножницах НГ-18 (рис. 71), НГ-30 (Россия), WEILIMQ 2031B (Китай) (рис. 72), CASATI ТO3100 (Италия) или бумагорезательных машинах.
Для раскроя рулонных материалов применяют также ротационные резательные устройства в виде вращающегося вала, на котором закреплен нож. Размер отрезаемых листов определяется частотой вращения вала и скоростью подачи материала.
Заготовки, получаемые в результате раскроя материалов, имеют размеры, превышающие размеры детали на величину припуска. Такие заготовки называют черновыми. Величина припуска зависит от вида материала, размера детали, точности оборудования, характера и условий обработки.
Рис. 71. Ножницы гильотинные НГ-18
Рис. 72. Станок для раскроя пакетов шпона WEILIMQ 2031B
5.8.4 Обработка черновых заготовок
Черновыми называют заготовки, имеющие припуск на усушку, строгание и торцовку. Чистовыми – заготовки, обработанные применительно к заданным размерам, имеющие базисные поверхности, расположенные под прямым углом одна к другой.
Черновые заготовки получаются в результате раскроя пиломатериалов и имеют в общем случае неправильную форму. У досок и брусков наблюдается поперечное и продольное коробление. Для надлежащей обработки деталей необходимо в первую очередь придать заготовке совершенно правильную форму, точные размеры и гладкую поверхность. Для этого необходимо выполнить следующие технологические операции: создание чистовых баз, обработка в размер по сечению и чистовое торцевание.
Точная обработка возможна только при наличии у заготовок чистовых баз, при помощи которых они могут быть точно установлены на станке для обработки. Для создания у заготовок чистовых базовых поверхностей пользуются в основном фуговальными станками (рис. 73). Фуговальные станки могут быть одно- и двухсторонними.
Рис. 73. Схема работы фуговального станка
На двухсторонних фуговальных станках обрабатывают одновременно две смежные стороны заготовки, расположенные под прямым углом друг к другу. Целью обработка на фуговальных станках – создание одной или двух смежных базовых поверхностей с получением между ними прямого или заданного угла. Нормальная заготовка полностью фугуется в среднем за два прохода. Толщина снимаемого слоя древесины – 1,5…2 мм.
Фуговальные станки c ручной подачей малопроизводительны, поэтому для фугования широких пластей крупных заготовок можно применять механическую подачу. Применяются следующие марки станков: СФ4-1Б (Россия) (рис. 74), Robland XSD-310 (Бельгия), ROJEK SD-B-510, ROJEK RFS410 (Чехия) (рис. 75), GRIGGIO COPMACT PF 41 (Италия) и др.
Рис. 74. Односторонний фуговальный станок с ручной подачей СФ4-1Б
Рис. 75. Фуговальный односторонний станок ROJEK RFS410
Чтобы обработать заготовку в размер по толщине, необходимо отфуговать ее вторую сторону, параллельную первой и расположенную от нее на определенном расстоянии. Такая обработка может быть выполнена по схеме: заготовка базируется обработанной стороной на плоскости и при поступательном движении на ножевой вал, расположенный на другой плоскости, параллельной первой, обрабатывается вторая сторона заготовки.
Чтобы обработать заготовку в размер по толщине и создать у нее параллельность сторон, применяются рейсмусовые станки (рис. 76).
Рис. 76. Схема работы рейсмусового станка: 1 – ножевой вал; 2 – стружколоматель; 3 – прижимная колодка; 4 – подающий рифленый валик; 5 – подающий гладкий валик; 6 – опорные валики; 7 – когтевая завеса
Наиболее широко распространены в промышленности односторонние рейсмусовые станки марок СР6-10 (Россия), СР8-2, ВЗ-350 (Беларусь), D-510 и D 630 фирмы ROBLAND (Бельгия), Griggio PS 43 (Италия) (рис. 77) и др. Также существуют двусторонние рейсмусовые станки С2Р8-2 и PRJG30 фирмы ROBLAND (Бельгия) и др. Последний снабжен предохранительным микровыключателем, индикатором размера заготовок, аспирационным колпакам, магнитной системой установки ножей, дробилкой отходов на подаче и выходе, цифровым программным управлением.
Рис. 77. Односторонний рейсмусовый станок Griggio PS 43
Высокая производительность при обработке заготовок с трех-четырех сторон получается на четырехсторонних строгальных станках (рис. 78). Наиболее распространены станки марок С16-4А, С20-2М, С25-2А (Россия), Weinig UNIMAT 23 EL (рис. 79), Weinig PROFIMAT-26S (Германия) и др. Эти станки имеют механическую подачу (вальцовую или гусеничную) и не менее четырех ножевых валов: два горизонтальных (верхний и нижний) для обработки пластей и два вертикальных – для обработки кромок заготовки. Большое распространение стали получать станки, сочетающие в себе фуговальный и четырехсторонний фрезерный.
Рис. 78. Схема четырехстороннего продольно-фрезерного станка: 1 – цепной конвейер; 2 – вертикальные ножевые головки; 3 – нижний ножевой вал; 4 – верхний ножевой вал; 5 – подающие валики; 6 – прижимы
Рис. 79. Четырехсторонний станок Weinig UNIMAT 23 EL
Обработка прямолинейных заготовок может быть выполнена на разных станках с различной точностью и с различной производительностью. При выборе варианта технологического процесса обработки следует ориентироваться на самые производительные станки, учитывая требуемую точность обработки. Варианты технологических процессов обработки черновых заготовок представлены в табл. 4.
Таблица 4
Варианты технологических процессов обработки черновых заготовок
Наиболее точная обработка будет получена по варианту 1, так как средняя точность обработки на фуговальном станке с последующей обработкой на рейсмусовом станке выше, чем у четырехсторонних фрезерных станков. Менее точная обработка будет по варианту 2, а еще менее – по варианту 4.
Торцевание заготовок производится для придания детали точной длины и для получения плоскостей достаточно ровных и расположенных перпендикулярно или под определенным углом к боковым граням (рис. 80, 81). Для этой цели применяются круглопильные торцовочные станки с одним, двумя или несколькими пильными дисками марок СТ - 404 (Россия), STROMAB TR 450 (рис. 82) и TR 600 (Италия).
Рис. 80. Схема торцевания заготовок на станке с кареткой:
1 – каретка с линейкой и упором; 2 – пила; 3 – направляющая линейка
Рис. 81. Схема двухстороннего торцовочного станка:
1 – пилы; 2 – конвейерная цепь; 3 – упоры; 4 – заготовки
Рис. 82. Торцовочный станок STROMAB TR-450
При больших объемах производства брусковых деталей целесообразно использовать высокопроизводительные автоматические линии, например автоматический торцовочный станок DIMTER OPTICUT S50 (Германия) (рис. 83).
Для обработки брусковых деталей применяются высокопроизводительные линии МОБ-1, ОК-508, ОК-503 (Россия) и угловые центры UNICONTROL 6 (рис. 84) и UNICONTROL 10 (Германия). Угловые центры предназначены для выполнения всего комплекса операций по изготовлению оконных рам с различными размерами и профилями. Станки этого класса отличаются не только высокой производительностью, но и хорошим качеством изделий, а также быстрой переналадкой агрегата.
Рис. 83. Универсальная торцовочная установка DIMTER OptiCut S50
Рис. 84. Угловой центр Unicontrol 6 WEINIG
studfiles.net
Листовые и плитные материалы: какие бывают, выбор и описание | Своими руками
Реклама
Многим из нас хорошо известны основные свойства например обычной фанеры – ее прочность, жесткость, стабильность и размеры.
Но, скорее всего, вы мало знакомы со свойствами других листовых материалов, появившихся в последние годы.
Неважно, какой проект вам предстоит изготовить, – мы поможем найти материал, идеально подходящий для ваших задач.
Улучшенные свойства благодаря современным разработкам
Все листовые и плитные материалы, включая фанеру, относятся к обширной категории искусственных древесных материалов. В отличие от натуральной, природной древесины, когда доски и брусья просто выпиливаются из древесного ствола и высушиваются, искусственные материалы получают путем дальнейшей обработки, добиваясь улучшения или изменения некоторых свойств.
Например, фанера состоит из множества тонких слоев, склеенных друг с другом так, что направление волокон каждого слоя перпендикулярно соседним. Это увеличивает прочность, уменьшает колебания размеров и позволяет использовать древесину с красивой текстурой только на внешних слоях.
Хотя фанера до сих пор доминирует на рынке, появляется все больше новых листовых материалов, производимых из стружки, опилок или размолотой в порошок древесины, которые смешиваются с клеем и специальными добавками, а затем прессуются. Гак изготавливаются широко известные древесно-стружечные и древесноволокнистые плиты (ДСП и МДФ). Даже традиционная фанера изменилась путем частичной замены внутренних или внешних слоев другими материалами, а становящаяся популярной фанера высокой плотности склеивается из множества очень тонких слоев шпона.
В статье описаны назначение и свойства десятка листовых и плитных материалов. Примечание.
Мы не стали включать в нее некоторые материалы, такие как ОСИ (ориентированно-стружечную плиту) и антисептированную фанеру, предназначенные для строительствва, а не для столярной работы.
Читайте также: Текстурирование дерева – как сделать красиво и правильно
Описание листовых материалов
- 1. Материал
- 2. Описание
- 3. Применение
- 4. Стандартные размеры
- 5. Сорта
- 6. Преимущества
- 7. Недостатки
Перечень:
1. Древесно-стружечная плита
2. Состоит из опилок и древесной муки со специальными добавками. Термическое прессование в листы и плиты.
3. Широко используется как подложка для напольных покрытий, для изготовления дешевой корпусной мебели. Ограниченно применяется в мастерских для изготовления некоторых приспособлений.
4. Листы и плиты толщиной 6; 12; 16; 19; 25 и 32 НИ.
5. PBU – для чернового пола M-S, М-1,М-2иМ-3-для изготовления корпусной мебели и столешниц.
6. Низкая стоимость и доступность, легкость обработки и относительная стабильность размеров.
7. Недостаточная жесткость, низкая влагостойкость. Крепеж удерживается плохо.
1. Древесно-стружечная плита с меламиновым покрытием (ЛДСП)
2. Одна или обе поверхности ДСП облицовываются бумагой, пропитанной меламиновыми смолами. На дешевых сортах пластик просто наклеивается, а на дорогих прочно связывается с основой путем нагрева.
3. Отлично подходит для изготовления корпусной мебели, так как пластиковая поверхность легко чистится. Используйте для изготовления приспособлений и простых фрезерных столов.
4. Листы и плиты размером 1250×2500 мм и толщиной 5; 12; 16 и 18 мм.
5. Стандартных градаций ЛДСП не существует, но есть так называемые «вертикальная» и «горизонтальная» разновидности. Дорогие сорта обычно имеют более толстую и прочную пленку покрытия.
6. Недорогой доступный материал с легко чистящейся поверхностью. Широкая гамма расцветок. Встречаются разновидности с покрытием из крафт-бумаги или натурального шпона.
7. Тяжелый материал с низкой влагостойкостью. Края распила часто повреждаются сколами при раскрое пильными дисками, не предназначенными для этого материала.
Ссылка по теме: Отделка шпоном, фанерование
1. Оргалит
2. Смесь молотых древесных волокон со смолами, спрессованная в листы. Одна или обе стороны листа могут быть гладкими.
3. Отлично подходит для изготовления самодельных приспособлений и мебели для мастерской, особенно разновидности с двумя гладкими сторонами. Перфорированный оргалит-удобное средство для подвески инструментов.
4. Листы толщиной 3 и б мм.
5. Черновой (2 зеленых полосы), стандартный (1 зеленая полоса), средней твердости (2 красных полосы), твердый (1 красная полоса), S1S (с одной гладкой стороной), S2S (с обеими гладкими сторонами).
6. Доступный и недорогой материал, легко обрабатывается, относительно стабилен, хорошо окрашивается.
7. Стандартный и черновой сорта не влагостойки, плохо шлифуются и плохо удерживают крепеж. Их края легко повреждаются.
1. Древесно-волокнистая плита средней плотности (МДФ)
2. Смесь целлюлозных волокон с синтетическими смолами, спрессованная при нагреве.
3. Отлично подходит для изготовления приспособлений, корпусной мебели, окрашиваемых изделий, отделочных профилей. Используется в качестве основы для наклейки шпона и пластиков.
4. Листы и плиты толщиной 6; 10; 12; 16; 19 и 22 мм размерами 1220×2440 и 1225×2500 мм.
5. Основная разновидность: Industrial. Дешевые сорта обозначаются маркой «В» или «shop». Также классифицируется по плотности: стандартная – MD, низкой плотности – LD.
6. Гладкие поверхности, отсутствие внутренних и наружных дефектов, стабильная толщина. Хорошо склеивается. Кромки легко обрабатываются.
7. Тяжелый материал. Обычные шурупы удерживаются плохо.
1. Хвойная фанера
2. Перекрестно склеенные слои шпона из древесины хвойных пород.
3. Садовая мебель, постройки и конструкции на открытом воздухе, мебель для мастерских, основание для напольных покрытий.
4. Листы и плиты толщиной 6; 10; 12; 16; 19 и 22 мм размерами 1220×2440 и 1225×2500 мм.
5. Сорта А, В, C,D (I,II, III, IV).
6. Дешевле фанеры из лиственных пород древесины. На первосортной фанере лицевой слой шпона часто имеет красивый рисунок текстуры.
7. Красивый внешний вид часто скрывает многие дефекты. Невысокая жесткость.
1. Кашированная фанера
2. Фанера с двухсторонним покрытием из плотной бумаги, пропитанной синтетическими смолами.
3. Широко применяется в наружной рекламе, подходит для построек и конструкций на открытом воздухе, окрашиваемых изделий, корпусной мебели, приспособлений и опалубки.
4. Листы и плиты толщиной 6; 8; 10; 12; 16 и 19 мм размерами 1220×2440 мм.
5. Классифицируется по сортам так же, как фанера из лиственных пород древесины. Внешние слои (оклеенные бумагой) из шпона сорта В (II) или А (I), внутренние слои из шпона сорта С (III).
6. Гладкие поверхности хорошо окрашиваются. Легко обрабатывается. Долговечный материал, устойчивый к атмосферным воздействиям.
7. Тяжелый материал. Ограниченная доступность.
1. Декоративная фанера
2. Фанера с наружными слоями шпона из ценных пород древесины.
3. Применяется для изготовления мебели и отделки интерьеров.
4. Листы толщиной 3;6; 10; 12; 16 и 19 мм.
5. Сорта шпона на лицевой стороне: АА, А, В, C/D/E на задней стороне: 1,2,3,4.
6. Стабильнее и дешевле массивной древесины. Отсутствие внешних дефектов на лицевой стороне. Красивый внешний вид.
7. Толстые листы могут быть тяжелыми. Тонкий шпон легко повредить. Кромки деталей приходится закрывать накладками.
1. Березовая фанера
2. Склеивается из тонких слоев шпона. В дорогих сортах отсутствуют внутренние дефекты.
3. Применяется для изготовления приспособлений, мебели, выдвижных ящиков.
4. Листы размером 1525×1525 мм и толщиной 4; 6; 5; 9; 12; 15 и 18 мм.
5. Сорта: АА, А, В, С, D.
6. Жесткость, стабильность, отсутствие дефектов. Хорошо удерживает шурупы. Обработанные кромки декоративны.
7. Тяжелый материал. Наружные слои только из березового шпона.
1. Фанера «Appleply»
2. Американская разновидность высококачественной березовой фанеры с наружными слоями шпона из древесины ценных пород.
3. Применяется так же, как европейская березовая фанера, преимущественно в декоративных целях.
4. Листы и плиты толщиной 6; 10; 13; 19; 25 и 32 мм размерами 1220×2440 мм.
5. Градации по сортам нет, но для внешних слоев используется шпон сорта «В» или «А».
6. Жесткость, стабильность, отсутствие дефектов. Хорошо удерживает крепеж. Разнообразие шпона на лицевых сторонах.
7. Ограниченная доступность, высокая стоимость.
1. Гибкая фанера
2. Все внутренние слои шпона перпендикулярны наружным, что позволяет изгибать фанеру поперек волокон наружного слоя.
3. Основное применение в качестве основы при изготовлении мебели.
4. Листы толщиной 3 и 10 мм размером 1220×2440 мм. По заказу изготавливаются листы другой толщины.
5. Изгибается по малым радиусам без растрескивания, не требует распаривания или поперечных пропилов.
6. Благодаря повышенной гибкости позволяет делать закругленные углы и декоративные формы.
7. Не применяется для нагруженных конструкций .Качество шпона на лицевых сторонах не нормируется.
Читайте также: Какие бывают краски – маркировки на банках и условное обозначение
Полезные советы для работы с листовыми материалами
1. Всегда тщательно измеряйте толщину листовых материалов, прежде чем выбрать пазы или шпунты в смежных деталях. Например, толщина фанеры часто бывает на 0,3-0,8 мм меньше номинальной.
2. Распиливая листовые материалы на пильном станке, располагайте их лицевой стороной вверх, чтобы избежать сколов. При раскрое циркулярной пилой их следует располагать лицевой стороной вниз.
З. Если вы часто имеете дело с листовыми материалами одного и того же типа, целесообразно приобрести пильные диски, предназначенные для этого материала, чтобы избежать сколов и получать чистые распилы.
4. Вместо того чтобы в одиночку управляться с тяжелым листом, пытаясь раскроить его на пильном станке, бросьте на пол 50-миллиметровую плиту из строительного пенопласта, положите лист сверху и раскроите его циркулярной пилой.
По материалам журнала для краснодеревщиков и столяров “ВудМастер”
Реклама
Ниже другие записи по теме "Как сделать своими руками - домохозяину!"
Подпишитесь на обновления в наших группах.



Будем друзьями!
kak-svoimi-rukami.com
Плиты и листовые материалы для устройства чернового пола

Устройство и утепление пола
Выравнивание пола является достаточно злободневным вопросом для большинства собравшихся основательно отремонтировать квартиру или загородный дом. Стратегия решения одна: ровный пол может быть только на ровном основании (черновом полу). А вот тактических решений как сделать основание пола ровным много.
Классическая технология выравнивания основания и устройства чернового пола с помощью лаг, поверх которых укладывают прочный листовой материал. Пустоты между лагами заполняют звукоизолирующим материалом. Если необходимо, для утепления пола укладывают слой теплоизоляции. Между плитами и изолирующим материалом предусматривают вентилируемое пространство.

Классическая технология выравнивания основания и устройства чернового пола с помощью лаг
Современный метод выравнивания и устройства чернового пола насыпным керамзитом, поверх которого настилают плиты из прочного листового материала. Лаги в этом случае отсутствуют, и выравнивание идет керамзитом мелкой фракции, что заметно упрощает работу. Но отсутствие под плитами вентилируемого пространства не позволяет использовать такую технологию для влажных помещений.

Современный метод выравнивания и устройства чернового пола насыпным керамзитом
Технологии и материалы для устройства чернового пола
Сразу внесем ясность: «мокрыми» называют технологии, в которых используют материалы на основе водосодержащих компонентов. Например, различные выравнивающие смеси. Они продаются в сыпучем виде и служат основой для получения раствора.
Выравнивание пола «сухим» методом, то есть без выравнивающего раствора, известно с незапамятных времен: черновой пол — по лагам, с утеплением и звукоизоляцией. Относительно недавно, появился еще один «сухой» метод устройства «чернового» пола, но уже без лаг: «черновой» пол настилается по предварительно выровненной керамзитовой засыпке (из мелкой и однородной фракции).
Отдавать предпочтение одному из “сухих” не хотелось бы: в каждом случае выравнивание основания под финишное покрытие пола может происходить одновременно с эффективным утеплением, звукоизоляцией и устройством отопления в полу, если это необходимо.
Нельзя не отметить, что новые конструкции черновых полов стали намного тоньше (35-40 мм): в них используются современные листовые материалы и непривычно тонкие рамные лаги. В результате, классический черновой пол стал вполне пригодным уже для помещений с высотой потолка от 2,7 м.
Как правило, современный черновой пол настилают из листового материала, в два слоя на клей, стягивая их саморезами. Материал укладывают так, чтобы получить между слоями разбежку по стыкам. Для этих целей можно применять гипсоволокнистую плиту, ЦСП, водостойкую фанеру, ДСП, МДФ и пробковые панели. Использование для этого досок, как вариант, не обеспечивающий ровного и стабильного основания, мы не рассматриваем, хотя половые доски никто не отменял.
Особого внимания заслуживают готовые элементы (двухслойные и трехслойные панели с фальцами) для устройства выравнивающего чернового пола. Предлагаются даже универсальные панели, укладываемые как на лаги, так и на выравнивающую засыпку. Кроме того, появилась новинка — элементы со встроенным звуко- и теплоизолирующим слоем. Конечно, такие элементы достаточно дороги, но зато заметно снижают трудозатраты и при работе не требуют большого профессионализма. Несмотря на разнообразие материалов для устройства «чернового» пола, они не столь уж универсальны, как может показаться. При выборе материала нужно исходить из целого ряда факторов.

Принципиальная схема устройства чернового пола: гидроизолирующая пленка, выравнивающая керамзитовая засыпка с уплотнением, теплоизоляция и «черновой» пол из листового материала.
Гипсоволокнистые плиты (ГВЛ, ГВЛВ)
Этот материал, как ни один другой, позволяет создавать ровное основание для чистового пола. Его настилают в два слоя на клей или уже готовыми элементами. Гипсоволокнистую плиту можно рекомендовать для метода выравнивания по керамзитовой засыпке или по звуко- и теплоизолирующим плитам. Пригоден он и для выравнивания существующего старого «чернового» пола: настилается сверху. Однако, недостаточная прочность к локальным нагрузкам (например, от ножек мебели) не позволяет использовать его в сочетании с лагами: можно проломить.
Если принимать во внимание возможные протечки (с верхнего этажа или аварии водопровода), то следует выбирать лишь влагостойкие марки этого материала и обязательно покрывать его гидрофобизируюшим составом. Но и в этом случае мы бы не рекомендовали его для помещений с повышенной влажностью. Такое основание подходит для любого напольного покрытия: паркет, ламинат, линолеум, ковролин, пробка и керамическая плитка.
Влагостойкое ДСП
Этот материал способен выдержать очень большие механические нагрузки и может укладываться как на рамные лаги, так и на выравнивающую засыпку. Имеет небольшой разброс по толщине и позволяет создать достаточно ровное основание. Обращаем ваше внимание на то, что это должно быть ДСП высокой плотности (используется в мебельных столешницах или подоконниках). ДСП обладает хорошими звуко- и теплоизолирующими характеристиками.
В Европе из ДСП делают готовые пазогребневые панели (в том числе и с дополнительными изолирующими слоями). Если использовать эти плиты, то их, как и гипсокартон, укладывают в два слоя на клей и покрывают гидрофобизируюшим составом. Если вы предъявляете особые требования к звукоизоляции пола, то сверху можно настелить (на клей) слой технической пробки. Рекомендуется применять ДСП лишь в сухих помещениях под настилку паркета, линолеума или ковролина.
Цементно-стружечная плита (ЦСП)
Этот материал, благодаря своим уникальным техническим характеристикам, находит все более широкое применение в современных строительных технологиях: не горюч, высокая механическая прочность, водостойкость и экологичность (цемент, известь и древесная стружка), при достаточно низкой цене. Выпускается разной толщины (от 10 до 32 мм). Применяется для изготовления «чернового» пола как в обычных, так и в помещениях с повышенной влажностью. ЦСП не страшны даже серьезные протечки.
Укладывать ЦСП можно как по рамным лагам, так и по выравнивающей засыпке. Настилается аналогично гипсоволокнистой плите: в два слоя, с разбежкой по швам и на клей (для керамической плитки). Верхний слой также покрывают гидрофобизирующим или гидроизолирующим (в помещениях с повышенной влажностью) составом. Пожалуй, единственным недостатком этого листового материала являются его отклонения по толщине (1-2 мм) на стыках панелей, что не всегда позволяет добиться идеально ровной поверхности, которая крайне необходима для таких напольных покрытий, как линолеум или пробка (неровности в стыках проступают). Однако, опытные мастера этот недостаток устраняют шлифовкой и выравнивающей шпаклевкой. На ЦСП хорошо укладывать паркет (в т. ч. штучный), ламинат, и керамическую плитку. ЦСП позволяет просто решить вопрос «отопления» в полу.
Влагостойкая фанера
Многослойная фанера имеет высокую механическую прочность и неплохую геометрию по толщине. Ее можно укладывать на рамные выравнивающие лаги. Многие отделочники настилают ее прямо на бетонные перекрытия под паркет или ламинат: пол становится теплее, но проблемы звукоизоляции фанера не решает. Материал этот достаточно дорогой, и многие, пытаясь сэкономить, берут невлагостойкую марку. Такая фанера (и без протечек) уже через несколько лет может начать расслаиваться. Во влажных помещениях этот материал не применяется. Подходит для паркета, ковролина и линолеума.
Древесноволокнистые плиты (ДВП)
Эти плиты (ДВП) отличаются высокой однородностью, точными размерами и механической прочностью. Позволяют создавать очень ровные основания, обладающие неплохой тепло- и звукоизоляцией. Но материал этот достаточно дорог. Несмотря на то, что ДВП устойчива к воздействию воды, применять ее во влажных помещениях не стоит. Подходит для настилки паркета, ковролина и линолеума.
Готовые панели и плиты для устройства чернового пола
![]() Панели из гипсоволокнистого картона и пенополистирола с фальцем не только создают ровное основание, но и делают его утепленным. На лагах не применяются. | ![]() Плиты из ДВП: имеют пазогребневое соединение, дающее ровный стык. Можно монтировать на лаги. Выдерживают локальные нагрузки. |
![]() Плиты из водостойкой ДСП с пазогребневым соединением остаются стабильными даже при значительной нагрузке. Их можно укладывать прямо на лаги. | ![]() Гипсоволокнистые плиты: с простым фальцем. Могут иметь различные изолирующие слои (минвата, пенополистирол). |
![]() ЦСП следует применять для чернового пола во влажных и пожароопасных помещениях. Ее можно настилать как на лаги, так и выравнивающую засыпку. |
Основные этапы работ обустройства чернового пола насыпным керамзитом
![]() Выравнивание, утепление и звукоизоляцию чернового пола можно выполнить керамзитовой засыпкой из мелкой и однородной фракции по его основанию. | ![]() Прежде чем настилать готовые панели, керамзитовую засыпку тщательно уплотняют. |
![]() Листы укладывают в два слоя и с разбежкой по их стыкам на выровненную керамзитовую засыпку. | ![]() Второй слой материала укладывают на соответствующий клей и стягивают саморезами. |
![]() Листы или плиты чернового пола плотно подбивают друг к другу. Необходимо полностью закрыть стыки. Оставшиеся щели заделывают шпаклевкой. | ![]() Листовой материал или готовые элементы для чернового пола подрезают в размер лишь у стены, оставляя между ними зазор для деформационного шва. |
![]() Целесообразно любой черновой пол обработать специальным гидрофобизирующим составом. |
Советы и тонкости устройства чернового пола
Лаги, подобно обрешетке под гипсокартон, выравнивают специальными дистанционными звукоизолирующими шайбами на саморезах. Если шайбы будут изготовлены из плотного звукоизолирующего материала (например, технической пробки), вы надежно защитите свою квартиру от шумов, передающихся по конструкциям.
Готовыми элементами можно устранить мелкие неровности старого чернового пола. Их склеивают по фальцам и стягивают саморезами.
Рамные лаги можно использовать в сочетании с готовыми элементами чернового пола. Неровности устраняют лагами. Пробка в верхнем слое создает хорошую звукоизоляцию.
В завершении, несколько видео по монтажу чернового пола, «сухим» методом, с использованием плит и листовых материалов.Устройство чернового пола на лагах из листов ДСП.
Устройство чернового пола с использованием керамзита для выравнивания основания пола. В качестве основания пола применяются гипсо-стружечные плиты (ГСП).
Что бы еще почитать?
remstd.ru
Как сделать ситцевый пол своими руками
Современный строительный рынок предлагает огромное количество напольных покрытий, подходящих для самых разных помещений. Плитка с дизайнерской росписью, наливные полы с 3D эффектом – чего только не придумали. К сожалению, такая роскошь не всем по карману, а создать эксклюзивный интерьер хочется каждому. Мы же хотим вам предложить сделать по-настоящему оригинальные полы, которые удивят всех ваших знакомых. Эти полы будут красивы, долговечны и недороги. А сделаны они будут из … ситца.
Принцип создания ситцевых полов
Ситцевые полы – это натянутое на пол полотно ситца, залитое несколькими слоями лака. Принцип создания ситцевого покрытия напоминает устройство наливных полов, только вместо графического рисунка используется ситец, а вместо полиуретановых составов – лак. В принципе, необязательно использовать для таких полов именно ситец, можно подобрать и другую плотную ткань (бязь, сатин, лен), главное, чтобы рисунок был четким и нравился вам.
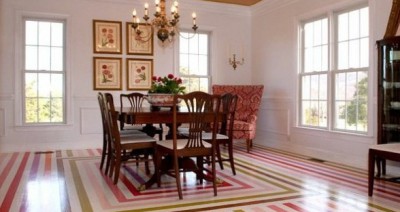
Ситцевые полы с четким геометрическим рисунком отлично украсят интерьер гостиной
Этап 1. Подготовка поверхности
Ситец – материал тонкий, поэтому основание для него должно быть идеально ровным. «Играющие» деревянные полы или вздутый линолеум категорически не подходят. При малейших дефектах лакированная поверхность ситцевого пола покроется сетью трещин, что не скажется положительно ни на его эстетике, ни на долговечности.
Для того, чтобы выровнять основание и подготовить его для оклейки ситцем, на пол уложите толстую фанеру, ДВП или ДСП. Листы тщательно подгоните между собой, чтобы в местах стыков не было перепадов высот. Швы зашпаклюйте, а затем зачистите наждачной бумагой. После этого основание покройте олифой, просушите и снова обработайте наждачной бумагой. Проследите, чтобы перед наклейкой ситца на основании не осталось пыли и мусора – для этого пройдитесь по полу пылесосом.
Этап 2. Наклеивание ситца
Полотнище ситца разрежьте на части необходимой длины. Для этого вам потребуется помощник, вместе с которым вы сможете натянуть полотно от стены до стены и нарезать нужное количество кусков.
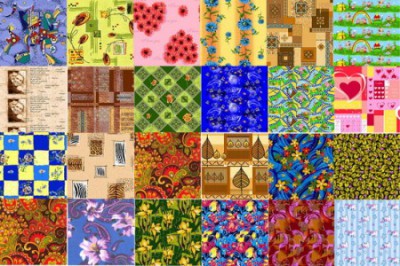
Вариантов рисунка и текстур возможно великое множество — на каждый вкус найдется что-то подходящее
На основание пола по ширине полотна нанесите тонким слоем клей ПВА или «Бустилат» и подождите, пока он подсохнет в течение 10-15 минут. После этого край полотнища ситца прибейте к полу маленькими гвоздиками и начинайте его приклеивать, разглаживая по всей длине с помощью валика, щетки или кухонной губки. Движения при этом должны быть направлены от центра к краям полотна, чтобы «выгнать» воздушные пузыри.
Проклеенную поверхность накройте хлопчатобумажной тканью и прогладьте горячим утюгом, у которого регулятор температуры выставлен на глажку хлопка.
Следующие части полотна наклеивают точно таким же образом, совмещая стыки и подгоняя рисунок.
В некоторых случаях, например, в небольшом помещении с правильной формой, прибегают к упрощенному варианту устройства ситцевых полов. При этом ситец не наклеивают на пол, а натягивают полотно и прибивают его по периметру небольшими гвоздиками.
Этап 3. Нанесение защитного слоя
После того, как весь ситец наклеен и просушен, необходимо покрыть его защитным слоем. В принципе, можно обойтись и без него, нанеся лак непосредственно на ситец. Однако в этом случае лак пропитает ткань и она потемнеет, изменив свой первоначальный вид. Это не слишком удобно, особенно если вы изначально подбирали ситец под цвет стен или потолка.
Защитный состав замешивают из 1 части ПВА и 4-х частей воды и наносят на ситцевое основание широкой кистью или валиком, равномерно смачивая ткань. После полного высыхания клея можно переходить к лакированию.
Этап 4. Нанесение лака
Лакирование ситцевого покрытия относится к наиболее ответственному этапу, от которого будет зависеть внешний вид пола. Для обработки следует выбрать качественный лак, образующий прозрачную пленку без эффекта желтизны. С этой стороны хорошо себя зарекомендовали алкидные и полиуретановые лаки. При выборе лака также стоит обратить внимание на стойкость к истиранию, чтобы не пришлось часто обновлять финишный слой.
Для получения прочного покрытия потребуется нанести на ситец 5-6 слоев лака. Это необходимо делать очень аккуратно при помощи поролонового валика. Следите, чтобы на покрытии не оставалось разводов и капель – нанесение должно быть максимально равномерным. Каждый последующий слой наносится только после полного затвердения предыдущего. Как правило, это происходит через 2-3 дня после нанесения. Самый последний слой сохнет еще дольше – 4-5 суток. Только после этого периода ситцевый пол можно эксплуатировать, не боясь появления вмятин, трещин, наплывов.
Весь период времени, пока производятся лакокрасочные работы, следует держать запертыми двери и окна, так как любой сквозняк или перепады температур могут вызвать появление трещин на лаковом слое.
По окончании работ по периметру помещения прибиваются плинтуса, окрашенные в тон ситцевому покрытию и покрытые лаком.
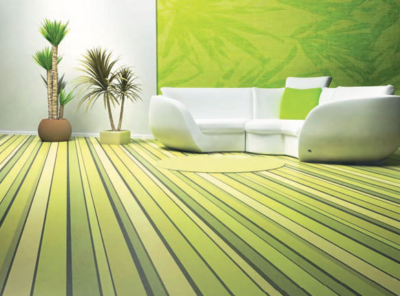
Ситцевые полы, выбранные в тон стенам, подчеркивают стиль и «воздушность» интерьера
Ситцевый пол иногда называют «ситцевым паркетом» и это не случайно: несмотря на тонкую воздушность ситца, в сочетании с лаком он образует довольно прочное и долговечное покрытие. Конечно, в ванной его устраивать не желательно, а вот в гостиной, спальне или даже кухне ситцевый пол станет оригинальной альтернативой обыденному линолеуму или ламинату.
Оцените статью: Поделитесь с друзьями!pol-master.com
Разновидности плит и листов для обшивки стен, пола и потолка

Разновидности плит и листов для обшивки стен, пола и потолка
Какие разновидности плит для строительства, ремонта и обшивки стен, пола и потолка существуют? Их особенности, достоинства и недостатки. Если взять для примера, каркасные дома, то долговечность и внешний вид таких домов напрямую зависят от используемых панелей для внутренней и наружной обшивки. Более того, применение панелей с готовой отделкой или слоем теплоизоляции (панель «сендвич») заметно сокращает и так непродолжительные сроки возведения сборно-каркасного дома.
ДСП
Древесно-стружечная плита изготавливается путем горячего прессования древесных стружек со связующими термоактивными смолами, которые составляют 6-18 % от массы стружки. Смолы экологически небезопасны, так как содержат вредный для человека формальдегид. По содержанию этого вещества ДСП разделяют на классы E1 и Е2. Более экологически безопасен класс E1, он разрешен к использованию в производстве даже детской мебели. Целиком облицованные ДСП-плиты не несут никакого вреда здоровью, вредное воздействие оказывают только открытые кромки. Новые технологии позволяют производить плиты класса Super Е, которые по всем санитарным нормам считаются безопасными. В целом материал отличается достаточно высокой плотностью, низкой стоимостью и простотой в обработке. ДСП обшивают стены, крыши, изготавливают перегородки, полы, используют в качестве основания под линолеум и ковровые покрытия.

ДСП Древесно-стружечная плита
Достоинства ДСП:
- широкая номенклатура цветов, рисунков, толщины;
- легко обрабатывается;
- однородность структуры.
Недостатки ДСП:
- плохо удерживает шурупы и гвозди, особенно при повторной сборке;
- уязвим для влаги;
- содержит канцерогены (например, меламин).
МДФ
Древесная плита средней плотности или древесноволокнистая плита сухого прессования. МДФ от английского (Medium Density Fiberboard). Изготавливается из древесной стружки, перемолотой в муку методом сухого прессования, при высоких температуре и давлении с добавлением вещества лигнин, который содержится в натуральной древесине. Лигнин делает этот материал экологически чистым и устойчивым к грибкам и микроорганизмам. Плиты МДФ бывают толщиной от 3 до 30 мм и ламинируются пластиками, лакируются или облицовываются шпоном. По влагостойкости и механическим характеристикам МДФ превосходят натуральное дерево и ДСП. Также МДФ в 2 раза прочнее и лучше держит шурупы. МДФ используется для отделки помещений, например, в виде стеновых панелей или ламинированного напольного покрытия — ламината, при производстве мебели, корпусов акустических систем. МДФ имеет однородную структуру, легко обрабатывается, очень прочная.

МДФ Древесная плита средней плотности или древесноволокнистая плита сухого прессования
Достоинства МДФ:
- огнестойкость;
- биостойкость;
- высокая прочность;
- лучше, чем ДСП держит шурупы;
- влагостойкость выше, чем у ДСП;
- широкий выбор цветов и рисунков благодаря покрытию пленками и шпоном.
Недостатки МДФ:
- горит с выделением ядовитого дыма;
- пылевидные опилки, образующиеся при обработке и распилке плит, вредны для здоровья.
Гипсокартон (ГКЛ)
По праву считается одним из самых популярных материалов для выравнивания стен, потолков и полов, устройства межкомнатных перегородок и даже элементов декора, таких как арки, колонны, сфероиды, многоуровневые потолочные покрытия и т.д. Основным компонентом гипсокартонных листов служит гипсовый наполнитель и это определяет многие положительные качества стройматериала. Так, гипсокартон химически инертен, его кислотность примерно равна кислотности человеческой кожи, он не содержит и не выделяет во внешнюю среду вредных для человека химических соединений. Стандартная плита на 93% состоит из двуводного гипса, 6% из картона и еще 1% приходится на поверхностно — активные вещества, крахмал и влагу.
Так, хрупкость панелей затрудняет их транспортировку, погрузочно-разгрузочные работы. По этой же причине ГКЛ не может выдерживать значительных физических нагрузок и не рекомендуется для выравнивания полов. Подвесные потолки из гипсокартона могут выдерживать вес не более чем 4 кг на метр квадратный, в то время как натяжные потолки способны нести нагрузку больше 100 кг на эту же единицу площади.

Гипсокартон
Разновидностью или более современной модификацией простого листа гипсокартона служит окрашенный или ламинированный гипсокартон, гипсовинил или гипсолам — гипсокартон цветной, с виниловым покрытием. Принципиально новый материал, имеющий изначально эксклюзивный внешний вид с широким выбором декора. Применяется для внутренней облицовки стен, для зашивки оконных откосов, создания перегородок, витрин и выставочных стеллажей, без дополнительной отделки.

Ламинированный гипсокартон, гипсовинил или гипсолам — гипсокартон цветной, оклеенный виниловым покрытием
Эти экологически чистые негорючие панели представляют собой гипсовую плиту, оклеенную с двух сторон специальным картоном. Имеют идеальную геометрию и используются для устройства внутренних перегородок и подшивки потолков. Поставляются в листах 2700 (3000) х 1200 х 12 мм. Выпускаются специальные марки гипсокартона для влажных (ванная комната) и пожароопасных (стена у камина) помещений. Они окрашены в «сигнальные» цвета — красный и зеленый. Есть гипсокартон и повышенной пластичности (толщина 6 мм, ширина 900 мм) для обшивки закругленных стен. На основе гипсокартона изготавливают панели «сэндвич» с теплоизолирующим слоем пенополиуретана (до 50 мм). Их используют уже для внутренней обшивки наружных стен без последующего утепления и пароизоляции. Это значительно сокращает сроки строительства.
Достоинства гипсокартона:
- экологическая и санитарная безопасность;
- легко обрабатывается: режется, сверлится;
- не горит, но при значительном нагреве разрушается;
Недостатки гипсокартона:
- низкая прочность, хрупкость;
- большая уязвимость для влаги даже влагостойкой разновидности;
- плохо переносит низкую температуру и значительные перепады температур;
- пригоден только для внутренней отделки.
Гипсоплита
Гипсоплиты практичный, современный и экологически безопасный материал, так как изготавливается без использования токсичных веществ из природного гипса, который не проводит электричества и не имеет запаха. Гипсоплита отвечает всем требованиям противопожарной безопасности. Гипсоплита, гипсовая пазогребневая плита (ПГП) является основным материалом при конструировании перегородок, подвесных потолков, различных декоративных выступов. Используется для выравнивания потолков, стен, «зашивки» систем коммуникаций. Гипсоплита бывает влагостойкой и стандартной. Стандартная используется в зданиях с нормальной влажностью. Для сырых помещений предназначены плиты с гидрофобными добавками. Такие плиты легко отличить по характерной зеленой окраске.

Гипсоплита, гипсовая пазогребневая плита (ПГП)
Достоинства гипсоплит:
- экологическая и санитарная безопасность;
- легко обрабатывается: режется, сверлится;
- мало горючий материал, класс горючести Г1
- относительно дешевая.
Недостатки гипсоплит:
- низкая прочность, хрупкость;
- большая уязвимость для влаги даже влагостойкой разновидности.
Гипсоволокнистый лист
Гипсоволокнистый лист (ГВЛ) – это современный экологически чистый гомогенный материал, обладающий отличными техническими характеристиками. Он производится методом полусухого прессования смеси гипса и целлюлозной макулатуры. По своим физическим свойствам гипсоволоконный лист представляет собой достаточно прочный, твердый материал, славящийся также своими огнеупорными качествами.
Гипсоволокнистый лист, благодаря своей универсальности, получил очень широкое распространение в строительной сфере. Применяется для устройства межкомнатных перегородок, стяжек полов, подвесных потолков, облицовки стен и огнезащиты конструкций. Популярностью пользуется ГВЛ для пола, который служит для сборки основания напольного покрытия, а также облицовочный вариант, при помощи которого обшиваются, к примеру, деревянные поверхности, за счет чего повышается их огнестойкость. В зависимости от области применения гипсоволокнистые листы подразделяют на два типа: ГВЛВ (влагостойкие) и ГВЛ (обычные).

Гипсоволокнистый лист. Укладка пола
Достоинства гипсоволокнистых листов:
- ГВЛ по сравнению с ГКЛ легче переносит распиловку в любом направлении, так как однороден по составу;
- Более высокая прочность за счет армирования целлюлозным волокном;
- Повышенная шумоизоляция.
Недостатки гипсоволокнистых листов:
- Менее прочен на изгиб, чем ГКЛ;
- Менее приспособлен для внутренней отделки, чем ГКЛ;
- Необходимость предварительной обработки перед покраской.
Цементно-стружечные плиты
Цементно-стружечные плиты (ЦСП) — идеальный материал для наружной обшивки каркаса и перегородок во влажных и огнеопасных помещениях, служит хорошим выравнивающим основанием для любых напольных покрытий. Имеет твердую и гладкую поверхность, штукатурится и облицовывается плиткой, пилится ножовкой, негорюч, устойчив к влаге и колебаниям температуры. Поставляется в листах 3600 х 1200 х 10 (12, 16, 20 и 26) мм.

Цементно-стружечные плиты
Фанера
Фанера является одним из наиболее распространенных материалов, широко применяемых в строительстве. Производство фанеры происходит путем склеивания нескольких слоев лущеного шпона фенолформальдегидными смолами. Для этой цели, как правило, используют березовый или хвойный шпон небольшой толщины. Выбор данных пород обусловлен их широким распространением в наших лесах: в Европе, Новой Зеландии и некоторых других странах для производства фанеры разных сортов широко используют дуб, клен, граб и даже грушу. Склеивание шпона осуществляется под давлением при повышенной температуре. Образовавшиеся в результате листы охлаждаются, и после непродолжительной вылежки собираются в упаковки по 10 или 20 штук.
В зависимости от древесины и клея, которые используются при производстве фанеры, она классифицируется на:
- фанера повышенной влагостойкости (ФСФ)
- фанера средней влагостойкости (ФК)
- фанера бакелизированная (БФ)

Фанера
Фанера ламинированная — представляет собой облицованную с одной или двух сторон бумагосмоляным покрытием фанеру. Данное покрытие весьма эффективно препятствует проникновению влаги, обладает высокой устойчивостью к стиранию и образованию плесени и грибков, устойчива к коррозии и разрушению. Данный тип фанеры благодаря ламинированию пользуется достаточной популярностью. При помощи ламинирования можно нанести практически любой рисунок или имитацию под: дуб, тополь, клён, березу, орех, сосну и лиственницу.

Фанера ламинированная
Достоинства фанеры:
- высокая прочность на разрыв и изгиб;
- отлично пилится, сверлится и скрепляется как гвоздями, так и шурупами;
- сравнительно недорогой материал.
Недостатки фанеры:
- смолы, используемые при склейке шпона, содержат довольно большую концентрацию фенольных соединений;
- горючесть;
Ориентированно-стружечная плита
Ориентированно-стружечная плита (ОСП — OSB), производимая методом прессования стружки толщиной до 0,7 мм и длиной до 140 мм под высоким давлением и температурой с применением небольшого количества склеивающей смолы. ОСП-плиты в 3 раза прочнее ДСП и МДФ-плит за счет расположения стружки продольно во внешних слоях и поперечно во внутренних. При такой прочности ОСП — материал очень гибкий и отлично используется при строительных и отделочных работах. ОСП-плитами различной толщины (от 6 до 30 мм) обшивают мансарды, потолки, стены, из них изготавливают черновые полы, опалубки, стеновые панели, ограждения и разборные конструкции. На пол под ламинат обычно используют самые тонкие плиты — 6 и 8 мм толщиной, для конструкций и опалубок более толстые — от 10 мм. ОСП-3 — это более прочная разновидность данного материала, используемая при малоэтажном строительстве в условиях повышенной влажности. Также из-за оригинальной текстуры ОСП является излюбленным материалом у декораторов и дизайнеров для отделки интерьеров. Из ОСП получается достаточно эффектное оформление потолка или элементов во встроенной мебели или в стенах.

ОСП Ориентированно-стружечная плита
На ряду с обычными плитами ОСП, есть и ОСП шпунтованная — плита с обработанными торцами паз — гребень, с 2-х или 4-х сторон.

ОСП шпунтованная — плита с обработанными торцами паз — гребень
Достоинства ОСП:
- прочность относительно других применяемых плит;
- влагостойкость выше, чем у ДСП и гипсоплиты;
- широкий размерный ряд;
- дешевле ДСП;
- хорошо держит шурупы, даже при повторном вкручивании.
Недостатки ОСП:
- обрабатывается хуже ДСП из-за неоднородности структуры;
- пыль, выделяющаяся при резке ОСП, раздражает слизистые оболочки носа, глаз.
- содержит формальдегид, особенно его много во влагостойких плитах.
Стекломагниевый лист
Стекломагниевый лист или стекломагнезитовый лист (СМЛ) белый, армированный стеклотканью, на 40 процентов легче ГВЛ, гибкий, прочный, огнеупорный, влагостойкий. Благодаря армирующей стеклотканной сетке СМЛ может гнуться с радиусом кривизны до трех метров. Это качество позволяет применять его на неровных поверхностях. Высокие влагостойкие качества позволяют использовать его в помещениях с повышенной влажностью. На лицевую сторону плиты допускается наклеивание любых отделочных материалов. При толщине листа 6мм он способен удерживать огонь в течение 2-х часов, выдерживает нагрев до 1500 градусов. Толщина листа: 3-20 мм.
Стекломагниевый лист (СМЛ) — универсальный листовой отделочный материал на основе магнезита и стекловолокна. Технология изготовления и состав материала придают ему такие качества, как гибкость, прочность, огнеупорность и влагостойкость. Его качества, позволяют применять его на неровных поверхностях и понижает возможность перелома листа при монтаже и переносе. Кроме того, этот материал экологически чистый, не содержит вредных веществ и асбеста, не выделяет токсических веществ даже при нагревании. В отличие от гипсокартона СМЛ-Премиум класса отностится к трудногорючим материалам (НГ).
Область применения стекломагниевого листа чрезвычайно высока. Как и из гипсокартона, из него можно делать потолки, стены и межкомнатные перегородки. Более того, с помощью стекломагнезитовых листов можно отделывать наружные фасады коттеджей и домов. СМЛ — надежная основа для любого вида отделки. Новый материал идеально подходит для душевых, саун, бассейнов — ведь стекломагниевый лист способен выдерживать высокую влажность, перепады температуры и открытый огонь. На поверхность СМЛ можно наносить самые разные виды шпатлевок, красок, клеев. Можно наклеить обои, алюминиево-композитные панели, шпон, пластик, керамическую, стеклянную или зеркальную плитку.
Лицевая (гладкая) поверхность листов предназначена для окрашивания, наклеивания обоев, ламинирования и нанесения различных видов декоративных текстур без предварительного, окончательного шпатлевания и грунтования всей поверхности материала. Тыльная (шероховатая) поверхность листов предназначена для прочной сцепки при приклеивании штучных облицовочных и декоративных материалов (керамической или кафельной плитки, шпона и т.п.), либо самого материала на стены и пол, склейке листов между собой. СМЛ может крепиться на крепежную систему, как из металла, так и из дерева. А также непосредственно на ограждающую конструкцию при помощи клея.
На ряду с обычными стекломагниевыми листами, в последнее время все чаще стали появляться ламинированные стекломагниевые листы с разнообразным рисунком и толщиной внешего покрытия.

СМЛ Стекломагниевый лист, стекломагнезитовый лист или стекломагнезит
Достоинства стекломагнезита:
- Влагостойкость — не подвергается деформации, не разбухает и не теряет своих свойств;
- Огнестойкость — магнезитные панели негорючий материал;
- Хорошая звукоизоляция — 12мм панель по звукопроницаемости соответствует четырем слоями двенадцати миллиметрового гипсокартонового листа, или кирпичной стены толщиной 150мм;
- Высокая прочность и гибкость — может гнуться с радиусом кривизны от 25 см до 3 метров;
- Легче аналогичных плит из дерева или гипса;
- Низкая теплопроводность, может использоваться как дополнительный утеплитель;
- Может применяться для отделки, как снаружи, так и изнутри.
Недостатки стекломагнезита:
- Более хрупкий, чем гипсоволокнистый лист;
- При шпатлевке стыков необходимо использовать шпатлевки на химических клеях;
- Свойства значительно разнятся в зависимости от производителя и класса СМЛ.
Фибролитовые плиты
Фибролит — это плитный материал, изготавливаемый прессованием специального древесного волокна (древесной шерсти) и неорганического вяжущего вещества (магнезиальное вяжущее). Волокно получают из отходов деревообрабатывающей промышленности, в результате обработки на деревострогательных станках. Один из плюсов фибролитовых плит – небольшой объемный вес. Фибролит отличается огнестойкостью: стружки пропитаны цементом, и при воздействии огня на них образуется лишь копоть. Материал допускает различные варианты отделки, легко крепится к любым конструкциям с помощью гвоздей, саморезов, дюбелей, легко поддается распилке.
Фибролитовые плиты — трудносгораемый, биостойкий материал, который применяют в качестве теплоизоляционного, конструкционно-теплоизоляционного и акустического материалов в строительных конструкциях зданий и сооружений с относительной влажностью воздуха не выше 75%.
Обычные фибролитовые плиты производятся толщиной 3-5 мм с использованием в качестве вяжущего серого цемента. Эти плиты применяются для различного рода термоизоляции, при устройстве кровельного покрытия и оштукатуренных перегородок. Акустические плиты обычно производятся из мелкой древесной шерсти (0,75-2 мм), что улучшает их внешний вид, ничем не закрываются, а также колеруются в цвета, гармонирующие с интерьером или производятся с использованием магнезита или белого цемента вместо серого. Композитная фибролитовая панель — это двух- или трехслойная панель со средним слоем из термоизоляционного материала, например, жесткой пены или минерального волокна (минеральная силикатная шерсть). Толщина среднего слоя обычно колеблется от 15 до 140 мм, хотя внешние слои фибролита имеют толщину от 5 до 20 мм. В этом случае уровень термоизоляции значительно увеличивается.

Фибролитовые плиты
Достоинства фибролитовых плит:
- Легкость монтажа;
- Хороший утеплитель;
- Механически прочный;
- Обширные декоративные возможности;
- Хорошая влагостойкость и огнестойкость;
- Звукоизоляция;
- Гигиеничность, безвредность здоровью человека и окружающей среды;
- Не портят грызуны и насекомые, не гниет.
Недостатки фибролитовых плит:
- Малая прочность на изгиб;
- Значительный вес.
Не стесняйтесь комментировать статью, если у Вас есть чем дополнить этот материал. Если Вы нашли ошибки или несоответствия. Возможно Вы знаете еще какой то аналогичный материал не представленный в этой статье?
Что бы еще почитать?
remstd.ru